MGI AlphaJet elevate Memjet Technology to a new level · Victor Abergel · Executive VP & MD
Imagine a digital printing machine that gives you fantastic print quality. Combine this with renowned digital enhance-quality, add digital hot-foil, and voila – here is the new MGI AlphaJet. AlphaJet has been under development for eight years, and development-cost a double-digit euro-amount, and here it suddenly is. INKISH was invited to an exclusive preview of the AlphaJet – and in this film, we will show you some of the new technologies introduced.
According to Victor Abergel, the AlphaJet has cracked the code to provide water-based inkjet on a wider range of substrates than most others. The paper is printed flat on a new transportation technology developed and patented by MGI. To keep the substrate stable during the entire process, printing takes place on top of 8 tons of granite.
The machine is huge, and so is the interest. MGI AlphaJet uses Memjet print heads, and for Memjet, this is the first time the company’s technology is utilized in a machine this size.
But watch, rather than read – we are certain that you will like what you see!
AlphaJET is our industrial print factory 4.0 concept that we will have the pleasure today to introduce to you.
We have started our development in 2012 of the AlphaJET. We have designed multi prototypes of the product. We are the only one who’s starting to approach the market with a full concept of factory 4.0. What does it mean? Factory 4.0? Meaning that we will be able to – with one equipment – replace three or four different conventional equipments. But as well to reduce drastically the resources to operating this technology and to be very efficient on the TCO for the projections. We are the first product which is bringing the printing to the finishing in one press. Printing operation – clearly the conventional equipments are there and are very efficient. We are reducing the turnaround very drastically. Even when we’re talking about folding carton. All right. But when we are finished to print, as I said before, it is just a commodity. When I need to do some finishing, I have to manipulate the substrate. I have to bring it to another stationary. This stationary goes six, seven times slower than the printing. We are doing the finishing. We have a service station for the finishing as well. With a very slowed down production time. And at the end, the bottle of the neck. When we are seeing a final product, it is not on the print, but it is on the complete process. Having analyzed that and due to the past of MGI. The experience of MGI. We have already bring on the market digital presses with the finishing inlined. We decided to rethink about our concept and to provide to the market today the complete solution from print to finishing in one operation. And that’s what I will have the pleasure to introduce to you today. To see from the CYMK print. We have used very new inkjet technology coming from Memjet, a water based ink technology. And to having the capabilities to manage substrate from 135 gsm up to two millimeter. With the capability to managing valuable data. As well on a print as on the finishing to be able to do versioning. On the print and on the finishing. And finishing what are we talking about. We are talking about spot varnish flat from 3 micron up to 230 microns. We are talking about digital hot foil with embossing effect from 3 micron up to 230 microns. So all this process supply on the folding carton for packaging. Suddenly you have something that nobody can do in 20 seconds or one minute. I can do a one print in a minute with all these different technologies applied.
What are your thoughts about the current marketspace?
Concerning the expectation of the market. Today, what we are able to see, that’s that the digital won the battle against the offset on the A3 size and B2 size. And the next battle that we filled in 2016 was the B1. Not only the format. We are talking also about the substrate, the folding carton, folding carton B1 was the next step. And which market are we addressing with those two parameters? We are addressing the packaging industry. And packaging industry is on demand because brand owners now are pushing the convertor to have new solutions for them. Where they can do versioning. Where they can do print on demand. Where they can do personalization. When they want to have short and medium run projections for reprint operations. And having this pushing from the brand owner and from the market. The converters are looking to finding a solution for them under the digital technology. And inkjet technology will be the one who can afford this problem. Why? Because toners or liquid toners cannot be applied on the very heavy stock. The only technology that can manage substrate like this, is the inkjet technology. And thanks for that. MGI is mastering this technology since a decade, two decades. And today we have the flagship coming on the market, our new AlphaJET product.
Why has MGI chosen Memjet for their printhead technology?
We choose a Memjet technology for several reasons. At the beginning, our first choice was to work with a UV inkjet technology. But we realized suddenly that it will be complicated due to the numbers of heads required to build an engine to cover the B1 size applications with the redundancy of nozzles required as well to avoid any missing drop during the printing process. To avoid the bending effect and the cost of the ink. So we were in a collaboration with Memjet since 2012. In 2016, we have been informed that they are bringing a new technology. The DuraLink technology. This printhead is 1,600 by 1,600 dpi. So that gives us a high definition. And with definition we can get as well a high grammage access with a deeper color. And covering in fact 90 percent of the Pantone colors on the CMYK process. And we decided also to test these heads and to integrate the heads in our technology. [00:06:52]We are finizio to a drop. Can you imagine a five year old up. [4.4s] If one nozzle is missing? We have full backup for the redundancy. So it’s exactly what we were looking for. To having a high quality printing engine. The assuring that we have no mark, no bending, no dual drop missing. Because on the printing process for packaging, quality has to be perfect. We decided to use the water based technology instead of UV technology for very good reason. First of all, water based technology is more eco friendly. And we know that in the future, the UV inks will have some problems with the approach of the friendly environmental approach. Secondly, the water based technology has a limitation concerning the subject. For that, we – thanks to our R&D department – find a solution to put inside of the machine and inline precoating inkjet solutions. Today the AlphaJET is virtually compatible with any type of substrates – paper and synthetic.
Why did you go for a flat conveyor system design with a marble base?
We had two choices. Or to do like the others – to using an offset chassis with a cylinder. And when you are looking at the Landa machine, when you are looking at HP technology, when you are looking even KM-1 from Konica Technology. All of them are using…or Komori chassis or a different chassis coming from offset manufacturers. What is the probability that using a cylinder technology where the paper to support some constraint in order to be printed? We decide to go on a different way. To having a flat conveying process. That’s why we are using and we have patented a new conveying process. Based on the linear motors. OK? We have checks with a vacuum system where the B1 sheet is dropped on, sucked by the system to be totally flat. We have 11 checks running on the ring on the linear motors. Linear motors give us an electronic and electro magnetic buffer where we have no vibration on the buffer, on the checks. And those checks when they are arriving under the printing process. We have a model of eight tons to avoid any vibration, to avoid any misregistration, to avoid any bending process during the printing. And today, yes, I think we made the right choice. Because having this ring [00:09:50]with those strips [1.3s] turning around. And the process to print, to embellish in one pass gives us a great stability. Gives us a great quality printing. And gives us as well high productivity for all this process in one.
Who will buy this machine?
We are addressing this product to the packaging industry. As well for the brand owner and for the convertor. We are seeing some sub market segmentations like commercial printing for a certain type of applications, which can be managed very easily. And as well for the web online printers. Or to the offering as well – packaging on demand. But other application can be managed by the AlphaJET.
When is the official unveiling of the AlphaJET?
We decided with our partner Konica Minolta to create a special exhibition center in Paris. To do the official kickoff of the AlphaJET. And we will invite worldwide customers, journalists to come to see. At the beginning of 2021. I mean, in January, to come to see the machine running. To come to have some workshop around the technology, around the concept and what can be the benefit and the added value of the AlphaJET in the industry.
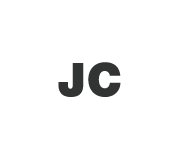

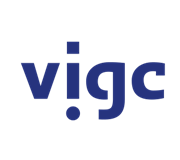

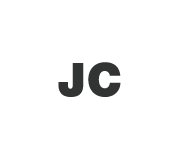

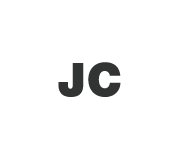

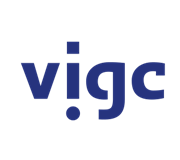

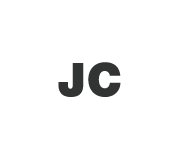

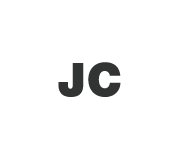

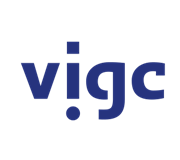

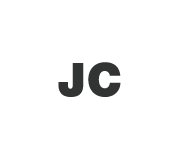
