INKISH.TV proudly presents: Deltabach · Amsterdam, Holland
LED-UV have in the recent time become more and more popular and it seems that both Deltabach and Billes Tryckeri (both covered here on INKISH.TV) is extremely happy with their new investments. In this episode INKISH.TV takes a look at the buying process, how long time the installation took and what advantages/disadvantages Marc de Jong sees with his relative new AMS LED-UV.
As usual, please watch, like and share.
Speed is everything.
You have to be quick as a printer.
I was wondering is that a real story.
In most cases you can earn back your investment within a year.
Deltabach is a print shop since 1970, making a lot of sheet offset work. Easy Print is just a web-shop providing everything with your logo on it.
What I always do is I go my own way and I don’t advise you that the general way is the way to go – that’s what I’ve learnt in the past 25 years. The kind of work we get is from agencies who are trying to get the best price at the specialists, and we are a specialist in some kind of that work.
I always want to get the best out of people and machines. In 2011 we bought the Heidelberg Speedmaster press and what I was seeing after a few years is that the operator was not always running at the highest possible speed. The print operators told me yet we have to slow down, because otherwise the product will not be good. I’ve always said: “Yeah, we have to wait, it’s not dry, low power speeds from 8,000-12,000”, but the machine can do 16,500/hour. And for me it was like who is lying – the machine or the operator.
I’m Jan Adolf from Wifac and I’m selling the KBA presses in Holland and the AMS LED UV units for the retrofit of all the machines we have in Holland. In the past the paper had to be dried. That is not the reason anymore to say that we cannot deliver today – you can deliver in any time of the day. Every printer has to buy AMS LED UV, because that is the best solution in the graphic industry at the moment.
I was surfing on the Net.
Marc has seen the AMS LED UV on the Internet.
And I read the story about LED UV.
He has a coder on the machine, but not so long delivery, so that was the reason for him to look for the solution to print faster. The big advantage is that the paper in the delivery is dry.
That opened my eyes.
You can print faster and your sheet break is not a problem anymore, because the paper is dried before it comes into the delivery.
Then we’ve visited a printer in Germany and it was a real story. Since we have LED UV there is no question about at what speed I can run at the press.
New machines are very expensive and by the way he is working now, he has 10-15% more production that he can make at the moment.
Production has gone up with 25%.
The biggest challenge is to convince the customer of the price of the system. AMS can also make a calculation for it and return on investment and when you look at that, in most cases you can earn back your investment within a year.
We want to earn back the installation in 3 years.
And that is based on, for example, the cleaning of the machine. In most of the times, the machine will be cleaned every week for two hours. When you calculate that on the year basis, that is 100 hours and then of course, your machine hours, you have more production and more profit in a year.
Most printers say: “Yeah, it’s nice, but the ink is triple the price”. That’s not really ink, but they don’t see the benefits, because they are used to that there are always stories. And what is the truth? The truth now is – it is the story.
Quality is better because the ink is laying on the surface of the paper, so you also use 15-20% less ink instead of the conventional inks, so that’s also an advantage, because the prices for the inks are a little bit higher 2-3 times, but you have to gain your profit from the way of working.
At Deltabach, AMS did it in a weekend. It is so easy – there are two brackets you place into the machine where you put a lamp in, there is a cooling unit, there is a computer and that’s all.
AMS came in on Sunday morning and on Monday we were printing again.
You have to reckon with approximately three days, the unit is installed within one day, and then you have to change your rollers, because they have to be UV-resistant.
We only had to remove the old rollers to UV rollers, and we did that on Friday night and on Saturday, so there was not really a loss of production.
The operator’s work is very quickly instructed. Two or three days is enough. The challenge was that in the beginning that lasted for 2-3 months, but now all the problems are solved and you see now how easy it is to work with the LED UV system of AMS.
You have to learn to print with UV inks.
We have helped Marc with it and he is using the right inks at the moment, because that was the problem in the beginning.
After 2 or 3 months, we did quite good. We found out they have to be more precise with the fountain and water solution – the LED UV range is a little bit smaller, but that is also with high-qualified printers. The quality of our print operators was already that high, so that was not a real issue. I think that when they are not at a high level, it’s more difficult.
All the problems with inks are solved.
After 4 or 5 months the operator has no conventional printing anymore, so there is no way back, I think.
He is also not working with his coding unit anymore, because that was what he used – dispersion coating only to protect the sheet, and that is not needed anymore. No more spray powder, as well. Another advantage of the AMS LED UV is that you can put an existing unit in your new press. That is a big advantage, because the unit holds for 20,000 hours, so when you want to replace your machine now, that can be easily done because you can put it in the new machine. That is not a problem at all.
We were used that there were about 30 or 40 pallets with printed papers waiting for transportation or our own bindery and now when we also produce for 24 hours, there are only 2 or 3 jobs waiting for processing or transportation. It gives us the position to install another safety under the press, and before LED UV there wasn’t a possibility because of the limited space.
It’s better for our clients because on uncoated stocks the print quality is better. The delivery time is why we as Deltabach excess behind companies we are competing with; most companies who are serious competitors with Deltabach are companies with 100-150 employees and we are only with 25. With the stuff you see here in our showroom, we compete with the big ones in Holland.
You have to be quick as a printer and you can do that with the AMS LED UV system.
We’re also faster in making decisions, because we are a little company. Now after 10 months, some clients are aware of what we can do and that we can deliver within a few hours.
Your paper is dry, your printing press will be a printer, no more powder, higher speed, better quality and faster production.
So, when a customer is calling you what we see is if customers are aware of where you can print in LED UV and deliver in a very short time. Now after 10 months, we also get jobs for that kind of printing. On Monday we have printed only a 1,000 A4 sheets, but they’ve called me at 10 o’clock in the morning, there was a meeting in the afternoon in a hotel at I think 3 o’clock, and it was the A4 that was in a range of other products printed in offset. I told them: “Why don’t you go to a print guy with an Indigo or iGen?”, and they said: “No, no, we only want the offset quality the same as we had before”. It has to be the same. So, at 2 o’clock in the afternoon, we’ve delivered it and it’s amazing how good they’ve paid for the job. If we get a name of doing those kinds of special jobs, it would be very profitable. There is a big company who is buying papers to print in later and they hear from their print houses who make the addresses on it that the printers have no problem with powder, because there is no powder. Our work is laying flat, so that customer told us: “In 2016, we’re going to buy all the stuff at your company and not at 2 or 3 other companies”, so the customer is tripling their turnover at Deltabach.
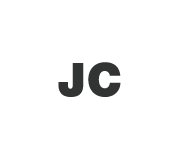

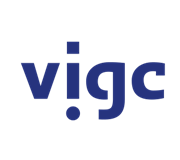

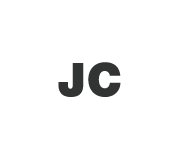

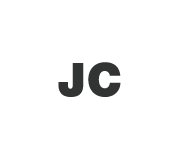

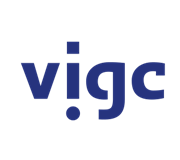

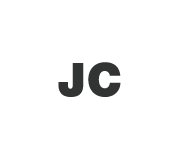

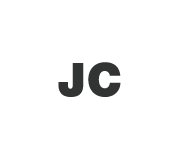

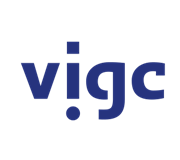

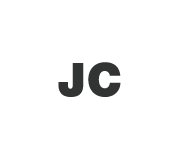
