Frank De Jonge · Over The Skypes · Adphos Group
Imagine a company born 30 years ago developing technology for space. Imagine a company that enables almost instant drying of ink by using light. Imagine a technology where the substrates aren’t heated, and where the dryer vaporizes the water from the ink at the speed of a snap, and enable a green and sustainable curring technology that can be used in all printing technologies where water is part of the ink-process. Ladies, and gentlemen – let me introduce Adphos. In this ‘Over the Skype’ your humble editor come short; fortunately, Sales Director Frank De Jonge is on solid ground and can explain not only the technology but also the applications where Adphos becomes a game-changer.
As with all our ‘Over the Skype’ interviews, quality is limited to bandwidth, web-cams, and ability to literally LIVE mix the conversations. However, it works, and with Over the Skype, we will bring you more than 20 exciting people, and angles on the industry as it is right now.
Enjoy!
Welcome back to yet another episode of Inkish over the Skype. This time we are back in Germany. And we’re going to talk to a very … I know you will agree with me shortly, we’re going to talk to a very exciting gentleman. His name is Frank De Jonge and he is working for an even more interesting company called Adphos. I would say that Adphos is maybe one of the companies that sometimes is a little bit behind the scene and you don’t see them that often. But that doesn’t mean that their technology isn’t really exciting. Anyway, so Frank, welcome to my show. I think it’s about time that you introduced both Adphos and yourself to my audience, please.
Thank you, Morten. I’ll start with Adphos. Your introduction is very right, we’re behind the scene. We are a component, but in many cases, a key component of printers, digital printers as well as flexo or rotogravure printers, whenever water and solvent needs to be evaporated in a fast pace. And often our technology is not seen, it’s hidden in the case of the printer manufacturer. And sometimes it’s also visible when it’s installed as a booster in a retrofit, an improvement of a certain print technology that already pre-existed.
I was thinking that you said to me the other day when we were preparing this, we will get into details in a second, but you even said that the box itself is a very, very, tiny little box compared to what it does, right?
It can be, yeah. A good example is a recent development we made for a textile manufacturer who’s replacing a 30 meter long drying length in a gas oven with a 1.35m long dryer of ours. Which is a factor of more than 25 times smaller. And we have the same amount of water evaporated without harming the substrate, in that case, the cotton textile.
Quite interesting. In your short introduction, you mentioned that vaporizing the water, and that is of course a key component in the drying techniques, just so people can put you in some kind of perspective, because I think that a lot of people they understand that you have IR drying, and you have powder, and you have UV, and you have gas heat, and you have a lot of different ways of making sure that the print you get out of your printing equipment is ready to process afterwards. But what is it that Adphos do that is so special to the market?
Let me start with gas. Gas is evaporating water with heat generated from fire or a kind of infrared light as well that can be emitted from a gas oven. It uses fossil energy, gas, and is no longer the drying technology of choice because of its CO2 emissions, etc.
The other three drying technologies you mentioned are all radiation. UV though is not drying, it’s causing a chemical reaction. It’s causing the photo initiators to film form with specific wavelengths of just below 400 nanometers. And near infrared, what we do, and infrared are electrically driven drying sources, radiation that evaporates water in different manners.
And infrared, just one more sentence, once infrared is heating the whole environment, the substrate as well as the ink, the NIR drying focuses clearly on the printed pattern, which is the ink. Which includes the water, could be solvent as well by the way, and the pigment. And we don’t necessarily heat up the substrate depending on the application.
So to put that in a … Because I’m apparently always the layman when I talk to all these exciting people, is that the result is that you have something that is dry when it comes out. And the ways of how it’s done and what that result is a little bit different. The purpose is, of course, to make sure that you can dry the substrate that you’re printing on, so you can have a good amount of ink, so you can get the densities high. As well as getting an output that you can process in your finishing equipment afterwards. That is correct, I hope?
That’s absolutely the target. And every application requires a dedicated approach. If we talk about printing on paper, which is kind of describing what you just said. We can get very close to the printhead. We can dry very fast. And take an example, 200 mm behind the printhead, a print speed of 300 meters means we start evaporating the inkdrop 40 milliseconds after it hit the paper. So really fast start of the evaporation process. And the ink doesn’t have a chance to penetrate into the fiber. It will just stay on top of the fiber. And that gives you the possibility to reduce your ink consumption because less pigment disappears in the fiber. You consume less ink, you’ve saved money on ink.
But also because the water doesn’t penetrate the fiber, it doesn’t hurt the fiber. The fiber doesn’t swell, and you don’t have this waviness in your books as you would have in a late stage drying or in a long drying process. Or particularly as well, like in infrared and gas, you heat the whole environment, including the substrate.
So that’s a key advantage. And it’s used by many book printers, particularly in the digital environment. Companies that we all know well, players in our market use our technology.
That’s fantastic. Adphos is an OEM but you also have an aftermarket, as I understand from you. But before we talk even more about the technology, and the thing is the market for this is of course you mentioned in the beginning that it’s not only in digital, it’s basically every technology that uses water based ink, right?
Yes. And other polar molecules. Water is a polar molecule and the solvent is a polar molecule in a wider sense. We evaporate alcohol with very high efficiency in any case. But then we have a little bit of a different construction because we need to be explosion proof. We are a water based system. We have an open module and an open drying system. But yes, in fact it can be compared a little bit with microwave. Where you heat up the water and your cup stays cool. And it’s very similar in the Adphos technology.
And when you got this idea and got started to develop this, how long time ago was that?
The kick starter of the technology was about 30 years ago now. In a project of the European Space Agency, ESA, the owner and founder of Adphos, Dr Bar, was running a group of scientists at the time who had to identify an energy source that can simulate the heat that is being generated when an aircraft, the space shuttle of the Europeans is what it really was, re-enters the earth’s atmosphere. The friction at that speed makes the surface very hot. And he identified NIR as being a very highly efficient energy source with a very high energy density per given space per square meter, if you want. And he developed that for many different applications. In the beginning it was more in the metal industry to be honest. And about now 23 years ago we were found by Scitex in our product for the inkjet printing industry. And we’re still a key component and, yeah, solution partner for Kodak.
And since you mentioned this exciting story from the European Space Agency, do you still have arms or fingers out into other industries? Or is it mainly something that comes to the print or reproduction technologies as we’re talking about now, or what is the business thing?
By 2020 the biggest portion of the business is printing. It’s grown over the last year. And it’s mainly because of the demand of highly efficient drying. In many machines, yeah, it’s a big market. And we win more and more printer manufacturers as our customers. Our technology is today also used in the automotive industry in car repair applications. All European car manufacturers except one use our technology.
It’s used in bottle forming, PET bottle forming, in very fast heating up PET polyethylene preformed to then put them into a blown form and make a PET bottle. And in the metal industry, where companies like ThyssenKrup and similar are using our drying technology in their metal painting and coating divisions in their factories as well.
Sounds fantastic. And what about when you look into the, I mean, obviously the advantages that we just spoke about in relation to the paper based and also other kind of substrates. The OEM thing, I mean, do you have competition, is it competing technologies or is NIR, it’s something that you own. Because, I mean, you said that you have found your way into a lot of printing equipment. But apparently not all. So I’m just wondering, is it because the people are using other technologies or what is the entrance for you in that segments?
Competitors are mainly the traditional technologies, as we just mentioned, gas and electrically driven infrared. That’s technologies that have been in the market for many, many years and decades. And that’s the other drying technologies. Not everybody uses Adphos, that’s true.
A big comparison, going back to the example from the textile industry earlier, is if you go and look for a, say, commercial print machine that runs at 150 meter per minute with an Adphos dryer. Compare it with an infrared or gas dryer, you will find the one with the Adphos dryer is about … Well, the dryer is one meter versus a 10 meter dryer in the other. So, that’s a big difference. And apart from quality aspects, etc, the size of the dryer makes a big difference. But of course other technologies have their reasons for being.
But again, in comparison with fossil energy driven drying technologies, what’s happening more and more is that companies invest in Adphos dryers and run them with regeneratively generated energy, electricity. Theoretically you can set up a windmill on your factory or a solar collector on your roof and drive your Adphos dryer with it completely CO2 free. And that trend plays quite into our cards really.
And then it also sounds like that you are in a good place in the market right now because there’s de facto growth in inkjet devices. There’s de facto interest in greener and more environmental products and services. So I think that you are on two trends, right?
Yes, that’s right. And I want to come back to your question from earlier when you asked for, you called it after market, we would call it booster or retrofit. Because retrofitting means typically an upgrade.
And it’s maybe a good example to take your first interview partner was Peter Sommer from Elanders.
That’s true.
And that was one of our first customers to boost his inkjet press that he had bought many moons ago. And it was running perfectly well on the standard book paper on an absorbing porous book paper. The dryer on board was drying the ink well enough because part of the liquid was staying in the paper as he rolled it up. And got it into his print treatment process. But then he started looking at, can I also print on offset paper on gloss paper, glossy, and where I have less absorption. And he very quickly found there’s limits in speed because the dryer on board wouldn’t be able to dry it all. And he had to bring down his productivity from 150 to less than 50 meter per minute.
Wow.
And in that instance, that’s an interesting printer because there’s CNYK stations plus a fifth station for the American NICR technology. Which in 98% of the cases is empty. So we designed a booster that we put into the fifth print station. And that’s only, in that first case it was 20 inch wide and less than 20 inches in printing length to fit into it, and it brought his printer back to the full production speed at any of the substrate he was using.
And Christophe Sommer, the son of Peter, actually made a very nice referral to this. And it’s still online on YouTube to look at. And we experienced quite nicely what it did to his application.
And when I hear stories like that, and I guess that also some of our viewers hopefully can relate to those kinds of stories, because I think that when we look at all the technology brought to market these days, I think that sometimes even vendors are a little bit surprised that the technology can be used in totally other ways than anticipated from the beginning. And when you have add-ons like Adphos where you can increase the speed, that basically means that the productivity of machine is, in this case, it was almost tripled, right? And then you get a way higher return on investment compared to what you could expect, right?
That’s a very quick return on investment he had because his productivity on his multi million machine investment came back for an oversee-able six digit number in a booster. Yeah. So, that product return was paid back very quickly.
Also in other applications, boosters were reasonable. I’m thinking of a Bible printer in the US who saved so much money on ink. Only on the ink because the penetration in the paper was so much reduced. He had his return on investment on ink saving in less than 18 months.
Yeah, I forgot about that, because of the cost of ink on the inkjet devices is relatively high compared to regular offsetting of course. So, of course if you can save both the ink and you can increase the productivity, it’s almost a formula to success.
Yes. There’s other aspects that we have not spoken about, when we look at the way of evaporating water without heating up the whole environment, without heating up the substrate. It has opened opportunities in the flexible packaging market where we can dry a water based ink, which can be food contact compliant, which are key important in the food packaging industry. We can dry that on a flexible film, which can be very thin, less than 30 microns at times, very temperature sensitive. And as a combination with the whole printing system and the drying system, we can keep the temperature below 60 degrees at any time. With temperature sensitive material like the flexible film, the alternative of drying water based ink is a very, very long drying tunnel with warm air. And I have to say, warm air, because 60 degrees is not even hot. And that’s, if you’re a sauna man, you know 60 degrees is not hot.
It’s not hot, that’s true. Frank, I think it’s very obvious that the technology that you have developed and that you’re selling has a lot of advantages. I was wondering, as you said, some vendors still use, I was just about to say legacy drying systems, but at least other drying systems. Do you see that your potential in the market is set to grow even more as an OEM partner or how do you see the future for Adphos?
If we take away the current crisis-
Let’s do that.
If we get that out of the picture. Yes, we see good growth opportunities. We have strong relationships with key partners in the printing industry. My role as sales director is to look after them and find more new customers for new applications. We are very keen to work in cooperation as a team partner with the ink manufacturer, the machine manufacturer, substrate manufacturer. That’s the key connections we have to deal with and develop solutions together. And that’s our target and that’s my role.
When you look at some of the technologies, one thing you said, we spoke about the different technologies for drying, but if you look at some of the manufacturers who have different print heads in the machine, I think that we mentioned last time we spoke, we talked about Memjet for example. Because that is also like with the waterfall technology, it’s a lot of ink on the paper at the same time. So I think that is also something where you really need to have a very good drying system in order to be able to use a lot of different substrates. Are you working with all kinds of technologies from [Sampa 00:19:30] print heads to Memjet to Rico or is it limited to some specific technologies in front of it or?
It’s limited to the desire of the printhead manufacturer to want to work with us. And that limit does actually not really exist. We have a good relationship to all print head manufacturers as they do water based. For example, it could be Seiko because they haven’t done water based so far until last year when they started bringing their RC1536A to market. And we demonstrated that in print with that printhead our drying technology with the white ink, one of the ink manufacturers that are using our technology.
In terms of both things, looking at the technology, at the science behind Adphos and infrared, it evaporates every liquid, every fluid where water is part of it, it will evaporate. The water evaporates, the solvent, and so we’re absolutely not limited to the head manufacturer. As we are not limited to the technology. Our drying is used in flexo printers, in rotogravure printers and wherever water and solvent needs evaporation, that’s where Adphos can be used.
Let’s change aspect of our story a little bit because I was thinking with being an OEM supplier, maybe I’m wrong, but because I see Adphos at all the trade shows. So that is not because I think you’re unknown from that perspective. But I was just wondering would the printers know you? Or is it something that is more like part of the solution? Because I think that if people don’t know that NIR and Adphos exist as part of the components that they should tick yes to when they invest in a machine.
And I’m asking because I’m a little bit curious about your go to market strategy and how you want to see yourself as a brand. Rather than just being something that you … I mean, I don’t know, for example, I have a Skoda car, I don’t know who delivers the brakes or who delivers the gasoline tank and the brakes and things like that. Because they OEM these from different part manufacturers. Do you see yourself as more as a part manufacturer entering into become a brand or how is your market go to in a market perspective?
Adphos stands for advanced photonic technologies, so we’re a technology provider. And we see ourselves as a technology partner mainly to the OEMs. Of course, we are open to the retrofitting to boosting solutions. Sometimes we do, not only sometimes, part of what we do is individual solutions, developing individual solutions for maybe a one off application in a very particular environment. This can be done. But a key part of our work is cooperation with the printer manufacturers. And you may not know the brakes manufacturer of your car, but Adphos as a brand also is not as well known as Intel. But Intel Inside is definitely a better comparison for how we see ourselves as a technology engineering solution provider in cooperation with the printer manufacturers.
I like that comparison better. I was just not fast enough. So sorry for that, Frank. But I was thinking in that relation that before Intel made that Intel Inside campaign, I think that was because they also faced the competitive situation from other processor manufacturers. And they wanted to make a brand so they could market themselves in a better way. And that is maybe more the question that I’m wondering. If people come to, let’s say, I want an X, Y set digital inkjet device and I would require it to have an Adphos dryer. That could be a brand strategy, right?
We just made a very interesting study because we have, not we have found out, we see since a long time, that the label industry is not using much water based ink. It’s only very few companies have, mainly using Memjet heads, come out with printers addressing the label industry. Which in our opinion is a big lack. It’s a big UV market if it’s digital. And UV cure is always, with the photonics, with the photonic cure inside, chemically, not always a 100% safe when it comes to food contact. And wherever UV cure is used, water based will always have the better toxic balance.
And we looked at the key suppliers of label printers in the Western world, put it that way, in the US and Europe. And we found that only three of them are currently not our partners. Or our cooperation partners in other areas, or in the label industry. So I believe we’re quite a well known company in this world. And with a reputation of providing high tech engineering solutions.
Yeah, I’m not questioning that at all. But as you said yourself right now, is that only three of these manufacturers are producing equipment for the food packaging label specific, right?
But label in general, not necessarily food, but label in general. Of course, our [inaudible 00:25:33] analysis and when it comes to food we see water based inks as the better solution.
Yeah. And that means that even though that you are partners with a lot of the vendors doing these machines that you still didn’t find your way into that. And I guess that is because the end customers, when they buy a machine, they maybe ask for specific UV curing or they maybe specifically ask for other kind of technologies. And then that was, when you look at … I think that for every brand you have your hotspot of where you are known by the public. I think that you had mentioned Intel yourself. I think that everybody in the computer industry knows about Intel, right? I’m not sure my mom does because she’s never been interested in investing in a computer specifically with that thing. And I was thinking that maybe, when you said about the label industry, where they may be less used to use water-based inks. It’s because they don’t relate that Adphos is that bridge?
That’s one of the jobs we’re currently tackling indeed. And that’s one of the next steps where we want to grow. Another industry where we want grow is the textile industry. Where that textile industry is quite under pressure with regards to CO2 generation as a whole. It’s the second biggest supplier of CO2 to our atmosphere right behind the oil industry worldwide, globally seen. So there’s big room for improvement. And we have started with several projects in the textile printing industry. And that will be evolved to other areas of playing as well in the textile industry.
So not only label is a rather new market and a growth market for us. Also textile is, whilst commercial or decor printing is already quite mature. In decor printing, there’s only, in Europe there is only one installation we know of that’s not using the Adphos drying technology when it is an inkjet.
It must be quite nice to be in that market situation as you’re describing it because, of course, you have to be a little smarter and a little, I don’t know how to say that, but you have to spend a lot of time finding customers. Because if you have all the customers already it must be … you should be smart finding anything. But it seems that you still believe that, I mean, you have a very positive approach to growth for Adphos. And I think that is, with the technology that you’re describing, it seems that it’s kind of a no brainer. So when you get to know what you’re capable of doing then the sales is probably a little bit easier, right?
We see a bigger awareness. We see also, as I just said about CO2 generation, is a big factor that drives into our direction. We see a bigger awareness, the presence on the trade shows and the conferences, the presentations we’re doing. It does give more knowledge about what we do and how we do it, and how we integrate it, etc. So yeah, we do see a positive and a good future for more evolution.
And the interesting thing is we’re a little bit upside down with concerned to the printing industry because we started in inkjet and we then moved back to the analog technology. Whereas all the rest of the printing world was the other way round. But we started in inkjet because the efficiency of drying so much more water compared to a flexo or rotogravure ink was required. And particularly when it was going into higher speeds, higher productivities. And then it was found to be an interesting technology also for other analog printing technologies.
When you look at the potential obstacles when you go to market with your products. Is it recognizing your technology or is it price concern or what is the obstacles when you … Because, I mean, everything you say about lower energy, you didn’t say lower energy, but the density of the energy and that you can use sustainable energy sources for drying and the environmental impact. And fast drying time and the non-chemical thing, I mean, all the things that you had mentioned in this conversation. Just wondering what is the obstacle? I mean, you’re sales director so you obviously from time to time meet people that, yeah, yeah, Frank, this is good, but, you know. So what is your opinion about that?
Let me take the example of the textile industry. The textile industry is very mature. It’s often in low cost countries. And it’s very price savvy. And so entering the textile industry with a rather expensive drying technology compared to what is currently known is not easy. It’s a bigger challenge than taking another part of the textile industry when we come to, for example, functional fabrics.
Yeah, fabric that … Imagine a curtain that has implanted led technology for those luxury hotels, these kinds of things are existing. They sell at a high price. They can either do their drying with a 15 meter long oven. Or they can use a 0.5m long Adphos dryer. And although the Adphos dryer is more expensive, it does give them the right effect, the right technology and the right solution in the application. And they’re much more open to consider this. And we are evolving with this.
Similar to printed electronic where a lot of Adphos dryers are used as well, again, on printed electronics, thermal temperature sensitive material is used, film is used. That’s where people don’t mind spending more money because it gives them immediately the right effect that they require. And if you compare that again with a flexo dryer, a flexo printer who has for the last 50 years used the same gas drying technology. And is used to it. It’s more difficult entering that space. You need the pioneers, you need the innovative people to start evaluating this.
And I’ve used an example today of one of the machine manufacturers. To one of the machine manufacturers, I said, “Look at yourself as an Audi, yeah. You have your technology, you burn diesel, you burn petrol, you’ve done that for the last 100 years. But now you have your e-tron. Yeah. And if you want to be on the top of the time, keep on offering your customer a gas dryer because he’s used to it, it’s easier to sell and it’s cheaper. But don’t forget to offer him a better technology. A CO2 saving technology, a space saving technology, electrically driven as an alternative.”
And I think that’s where we are in many industries now. And we are in a phase where we would say without corona we would see a faster, steeper growth into newer segments. Corona may, or the financial crisis following this, may be a hindrance in new investments though.
But that makes a lot of sense because all you say is of course about when you come from a, let’s say, that you are, for example, in third countries where you talked about the textile industry, it makes perfect sense that it’s a longer selling cycle. And you need to maybe even create a demand from the buyers that they want to have something that is more environmental friendly and all these things.
And that’s why I like your story from Elanders in the beginning of this conversation because that kind of demonstrated that there was an instant return on investment by adding, even though it was maybe an expensive add on to it, but the ROI both on the machine that you delivered, as well as on the HP machine was … I don’t know the repayment type of these things, but tripling your utilization and productivity, and at the same time also saving ink. It seems almost like a no brainer as I said before. So I think it has given me a good understanding.
I’m sorry that I am not trying to be ignorant in asking the stupid questions. I just didn’t know much about Adphos so I apologize for my lack of knowledge ahead. Because I think this is really, really exciting to get to know this.
I still feel stupid when I see some of the results that we are achieving. And this booster thing is a good thing. I talked about individual solutions, sometimes we … Not long ago we created a dryer for a 2.20 meter wide coating line. That coating line is able to coat at 150 meters per minute. But it runs at 20. It’s the nature of this technology. It’s not perfect. It’s coating, it’s a specialty thing. And it’s got a 40 meter long oven today. And coatings of 750 mm thickness. We can speed this up on one meter. Basically it’s a 25% productivity gain, five meters more per minute by an additional one meter dryer to the existing 40 meter line. And I’m stupid. I sometimes don’t understand this as well, but it does work. The technology does what it promises. And it’s quite exciting selling this additional value to customers who appreciate this.
And Frank, to be honest, I appreciate the last 36 minutes with you. And I want to thank you very much for participating in my old Skype session here. I can guarantee you that when this is over, the corona crisis, then I would like to meet with you and your team. Because on a purely editorial basis, I would like to know more about this to understand it. Because I think it’s a fantastic technology that you are providing. So thank you very much for your time. And stay healthy and all the best.
You’re very welcome. Thank you for your time and you’re always welcome to our headquarters in Bruckmuhler, between Munich and the Alps. You will find a nice environment as well.
I look forward to see you.
Thank you, Morten, Likewise.
Yes, bye bye.
Bye.
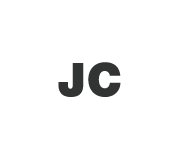

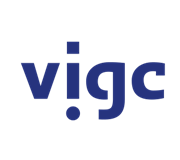

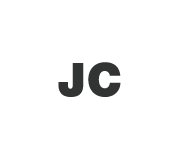

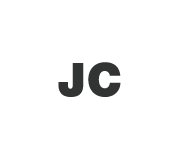

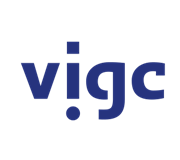

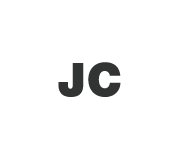

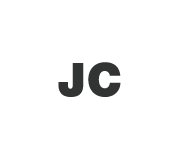

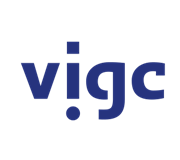

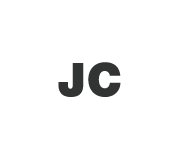
