INKISH.TV proudly presents: Business Development Manager, Elsa Callini
This episode was recorded a long time ago – not because we didn’t find it interesting, but since we wanted to be able to explain ebeam technology as good as we could. In the video Business Development Manager, Elsa Callini, and VP Global Sales, Karl Swanson explains the technology and the potential of the new closed loop ebeam retrofitting solution the company offers.
ebeam Technologies develop and manufacture electron ebeam hardware.
ebeam technology has many applications, but the one we were interested in and was presented at Drupa is printing.
The ebeam systems that we’ve been building up until now have been much more traditional in terms of their size and scope and capabilities, which we’re excited. We’ve got two of those systems running at this show, one on other printing methods on offset lines and flexo line. What we’re introducing at the show is the world’s most compact ebeam system, which really is a great fit for the inkjet printing market, and that’s what we’re excited to show here.
So this setup also follows the trends of label and packaging?
We’re really excited about the trend moving towards digital printing. It’s becoming a dominant part of the industry, and as you pointed out, people who have been making labels or doing other kinds of printing on narrow web lines are looking for the opportunities available to them in the food packaging area. And, the combination of ebeam and inkjet printing fits that very well, and that’s what we’re looking for.
Let’s get into the technical stuff. How does this actually work?
So, ebeam is a new way to cure or dry the inks. That’s what ebeam does for the printing industry. Everything starts here when we emit electrons, when we produce an electron beam. And, this is our lamp. That’s what we call a ìlampî, because it’s a sealed way of producing electrons. So, ebeam has been used for several years, and ebeam technology has different products in this portfolio, from sealed lamps to bigger instruments. But, the way of producing electrons is always the same. So, we start from a cathode. So, it’s a filament. It’s a tungsten filament where we produce electrons, and these electrons are accelerated. So, from the cathode inside here to the window here, there is a voltage difference. Therefore, the electrons are accelerated.
Here, you can see a titanium foil, and that’s the magic of our e-technology. This thin titanium foil can let the electrons go through, and therefore go in towards your substrate where the ink is, and where you can cure your ink. But, it prevents the contact between the air outside, atmospheric pressure, and the vacuum inside. The difference between the big systems and the little lamp is that, the big systems need a constant pump, pumping system, as well. The windows are way bigger. In this case instead, it’s a sealed system. Therefore, it means that once the lamp is pumped, the copper wire is clamped and the vacuum stays inside. So, we do not need a pumping system close to the lamp. That’s why we can create the most compact ebeam system in the world.
The difference in voltage means that the electro are accelerated, and you have to think of electrons as balls that we throw to a substrate. So, according to how much power or energy or strength we put into the ball, the ball can go deeper or stay at the surface, and that’s the great advantage of electrons. We can tune the acceleration voltage, and therefore we can tune the penetration depth of the electrons into the substrate. The other thing is the effect of the electrons when they reach the substrate. In that case, the electrons have the strength to break and create bonds, what we call polymerization effect, and therefore the inks, which are glue-sy or in the case of inkjet, like water, they become completely dry. And, that’s also why we do not need photo initiators, because the electrons have energy enough to make this reaction happen.
And that makes the final product food safe?
This is the great advantage of using ebeam technology. We do not need photo initiators because electrons have already the energy enough to create these bonds, to create this polymerization effect. And, we can create printed packaging, which are food safe.
So, this is exactly the same lamp that you saw there, just turned. And, this is the titanium foil, the window where the electrons are coming through. Here is the lamp, the filament, the cathode, where the electrons are emitted, accelerated, and the titanium foil prevents the vacuum to be in contact with the atmospheric pressure.
This is actually a patented technology from our company, ebeam technology. This roll, it’s a shielding roll. So, the distance between the lamp and the shielding roll, it’s actually adjusted so that no other shield is required for the machine to be operated, but it’s close enough for the electrons to have the best effect, the strongest effect on the substrate. This can also be adjusted, of course when we integrate this module in existing lines, this can absolutely be adjusted.
Now let’s look at it from a business perspective
Because at the end of the day, of course it matters what the return is on the investment that the customer’s making. So, what we’re offering is a technology where they cannot only achieve the food safe requirements so they can be certain of eliminating possibilities for failed products or return products, they have more security in their operations in that regard. We’re doing all of that in a platform with low operating costs, very energy efficient process, and even lower operating costs as the ink costs will be the same or less than competitive methods that are available.
What do you mean by competitive methods?
I referring more about competitive technologies. And predominantly, UV is the one we’re most similar with and most compared against. And so, in that regard, both in terms of the electric power consumption, ebeam is much more efficient in that regard, and when it comes to the ink costs, because the photo initiator that’s removed for an e-beam formulation is one of the more expensive components of a UV ink. So inherently, we have an advantage there as well.
Talking about inkÖ does this technology require a specific type of ink?
We need energy curable inks. It’s the same with UV. UV is another type of energy curable process or inks for UV are energy curable, so we need the same process inside the inks just without the photo initiators. So, it’s actually even better.
this demonstration, we worked with partners from Collins Inkjet in the US, who have really taken the lead in producing electron beam curable inkjet inks. I can also tell you there are certainly others that are also looking at this combination, and doing their development work related to this.
Are you facing any obstacles in bringing this product to market?
Right now, the primary obstacle still is, I think is at the level of awareness and understanding of the technology. It’s a new concept, a slightly different idea than what they’re most acquainted with. So, much of the time is explaining the fundamentals, filling out the picture for what might be involved with implementing this technology.
Do you think there is a high demand on the market for different alternatives like this one?
If you see how much attention we drove here in these past two days, you can really feel that people needed this solution. They were looking for this type of combination. They were looking for this type of compact system. They were looking for a solution that could actually be affordable and really user friendly. And, they really needed an alternative to the current technology, and that’s what we are offering here.
What do you think about Drupa? Was it good for you so far?
First few days have been fantastic. I mean, the booth traffic that has come by has been outstanding, the specific interest in this combination has been very rewarding, and we’ve even had customers bring in materials for us to try printing on. We’ve done those trials on the fly here at the show with good results. So, it’s been quite exciting.
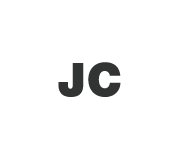

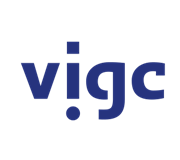

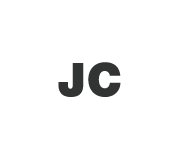

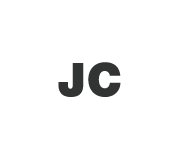

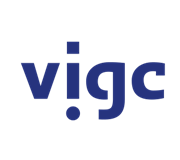

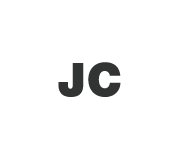

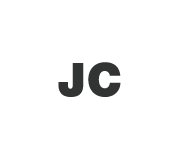

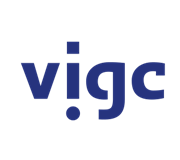

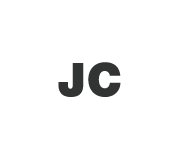
