INKISH.TV proudly presents: Harm Jan Hulleman ยท Area Manager ยท Tecnau ยท Italy
At the Argos Inspiration Days 2018, Area Manager Harm Jan Hulleman gave a presentation of Tecnau’s ingenious products made for commercial book production as well as on-demand production.
About Tecnau, we are family owned company headquartered in Ivrea in the north of Italy. Basically, what we do is we offer solutions around digital print. So there’s a huge, big printer in the middle, we don’t do that. We do all the machines before the printer and the machines after the printer. Our goal is actually not to make machines that bring down the cost or make you more efficient or make you go faster, or do things cheaper. Actually what we try to do is to bring something extra to digital print. Therefore, also our tech line and empowering digital print. We want to do more with all the capabilities that digital print offer you today. Some of the solutions you will see later on in my presentations, for instance on the right, this is a book block making line. The end product there is a unique book block for really being able to print book of one. This line is worldwide unique in its flexibility and the capability of run different book sizes randomly through each other.
The solution on the left is also another example of how we try to empower digital print. How we’re try to bring new things to the market. This is a roll changing module. So, if you print from a roll, the roll is empty, you need to change the roll, it cost you 4 or 5 minutes. This machine does it automatically on the fly without stopping the printer. Now that as such, is not really new. There are other solutions like that on the market. What is new with this solution, is that it can actually hold two different media types. It can change from one media to the other on the fly in the middle of your print job. I will come back a little bit later on. Skip that.
So about Tecnau, we offer solutions in a wide range of different market segments. We come traditionally from the transactional print market, from the banks, the insurance companies, to governments tax authorizations. Things like that. That market is still interesting, still important for us today. We have a lot customers in there, however it’s not the really growing market. It’s actually little bit saturated market. It’s not where we expect the growth in the coming few years. Really what a growth is, is in graphic arts. Within graphic arts there’s a couple of segments that already today show a huge growth rate. For instance, book printing and also the photo segment offered some interesting possibilities. So that’s where we focusing on.
With in Tecnau as I mentioned we are a family owned company headquartered in Ivrea, in Italy. We have about 230 people all over the world. We are quite internationally organized to be honest. So we have three different production facilities. One in Italy. One in the South of Sweden, in [inaudible 00:02:51], and another facilities in Billerica just outside of Boston U.S. Out of the 230 people, there’s about 55 people that are on a daily basis involved in product development and engineer. That is a relatively high number for a company of our size. That comes also back a little bit to the engineering background within Tecnau. We like to develop new things too. We are able also to make customized things, or unique bespoke solutions for certain customer applications. Over that we are worldwide supported by a distributor network. We have our own technical service people around the world for third level service support. In some countries we work direct. For instance, in the U.S. we have our own sales force, were as in other countries we work either through a distributor or in very close relationship with the print department.
Looking at solutions in the different market segments, obviously in transactional print, it’s relatively straight forward. A lot of roll to roll solutions. Roll to fanfold, roll to cut stack. One of the real strength of Tecnau is our dynamic perforating and dynamic punching solution. Based on reading mark we make a certain perforation in the web for a certain punch pattern in web. Tecnau invented this many years ago and still today, we are by far leading that market with our solutions there. In graphic arts it’s a very wide range of solutions we offer. Some certain book solutions around what we call the libra family of products, but we also have some very unique solutions around photo, around calender, postal cards and things like that.
One of the key things within … Let’s say overall our product lines, is the high level of automation and flexibility within the equipment. Being able to adjust or cut different sizes or stack different sizes, or fold different sizes on the fly without having to reset the machine, or without having an operator on the machine. All of these products are guarded by two other things. One is the web vision camera control system, which is a unit that can be placed in any line looking at the complete web, at every single page in the web, and doing a lot of different inspections on the web, front and back side, looks at color, looks at positioning. It can check whether the perforation has been done correctly. It can look at the registering … All sorts of things depending on the software level that you have.
The machine comes in an ex spec version, meaning as a separate standalone unit that can be placed in any line basically, or as an in spec version where actually we build it inside the ink head printers assuming there is space for that. There’s an on spec version where we basically take the cameras and build it on one of our existing machines. The other solution is the Tecnau connect, which is basically a tool that collects a lot of data on your production. For instance, based on reading data matrix for barcodes. It collects that and analysis that and can report it also later on. It also offers you a central point of operation, especially when the lines become very, very long and very complex with a lot of different modules in there. Sometimes not even from one offender, but a mix of different companies building a line together. This allows an operator to have an overview of what’s happening in the line.
As mentioned before, we have a huge variety of different products and machines around there. I will not go through all of them. If you are interested we have a little stand in the middle here in the room, so feel free to come over later on and ask some questions. I’ll just focus on a few of the newer things, so the more common things. Last year we introduced a new series of unwind, rewind products called the u9 r9’s. Here you see a picture in combination with a Xerox driver. The u9 r9 are slightly heavier built and have a bigger diameter in rolls. It can handle also a little bit heavier and bigger rolls, but the main difference here is that the machines are tight web units as most of the new printers that come out today are basically requiring a tight web, a certain web tension, which also makes the machine easier to use.
Some of the things that are also changed, is also the fact that we support with these machines, a much wider media rate. So, we go from 40 gsm all the way up to about 300 gsm paper. This is all settable by the operator through the display, so no mechanical change is needed anymore. As mentioned before, the splice is a really unique solution. Initially, basically, if you look at an average printer today running about 130, 150 meters a minute, if you take and average roll size of one meter 20, it will take you about 90 to 100 meters to run that roll. Then if you have a trained engineer, or trained operator I should say, it takes him about four, five minutes maybe to change the roll if he is there and if the roll is prepared and if he doesn’t have something else to do at that moment. The reality learns that the operator is busy on another line or the roll is not ready, or he’s just having a coffee break and in reality the printer stands still for about ten 10 to 15 minutes.
By having an automatic roll changer, the printer keeps printing, the roll is changed automatically on the fly by just cutting the web, adding the other web to the original web by having a little bit of glue in between and we put the two webs on top of each other. We don’t really actually splice it, but we glue the two webs to each other. This all happens on the fly. No stop is needed. Basically you win between 10, 15 minutes every 90 minutes, so overall a productivity increase of about 10, 15 percent. Now that’s nice as such, but we think a little bit further, and a little bit outside of the box, or the roll in this case, and we make this possible to have two different media types.
For instance, roll A is a white paper 80 gsm and roll B is a yellowish paper 110 gsm. Based on a signal from the printer, in the middle of a job, we can actually say, splice. We change from roll A to roll B and suddenly the printer is printing with a different media type. Until it’s finished, the job is done. The printer tells us again to change back and we go back. Splice again, and now we’re running with roll A again. On the fly, without stopping, we’ve gone back and forth, back and forth. This is truly unique in the world. No other solution out there can do this today.
Perforating and punching on the left you see some examples. This can now be done on the fly just by reading a dot matrix. As mentioned, Tecnau is one of the leaders in that market. We invented the dynamic perforators years ago. Today we offer two series, the 1550 series which is now the HS meaning high speed, so supporting speeds all the way up to about 240 meters a minute as well as the 8,000 series. A whole range of different machines in there with also field gradable possibilities. Lot of different possibilities are available when it comes to dynamic perforating and dynamic punching. This was all based on web printing, on continuous feed printers. We have now also taken that technology and I will come back to that later on at the end of my presentation and we have moved that into the cut sheet arena. We can also support dynamic perforating and punching in combination with cut sheet printers.
Sheeted output going from roll to the printer and then cutting and stacking and delivering different stacks. What we have recently announced is the 566 wide, which basically means we now support a 22 inch web width, 560 millimeters. As more and more of the new printers that are coming out actually support the same web width and it allows you to print certain book sizes, or job sizes in either three Op, or possibly even four Op. That’s quite new. Still today, the 2320 is the most common, the most popular roll to cut stack line. It offers rotative technology, so cutting technology, but there is two rotative cutting knives in the machine, which then allows you to make a strip cut. You can actually cut away a certain programmable strip size which is then going into the waste extraction unit. Supports one Op, two Op, three Op’s all the things automatic size change on the fly. That’s still there.
Some of the newer things is more related to the stacking. A new solution that was brought to the market, about two years agon now, is the high capacity stacker, which is an extra unit, which is placed after the existing of a stacker. It allows you to not only cut and stack long sheets, but also to cut and stack them on a very high pile. So you’re stacking the long sheets directly onto a trolley or a pallet, and when the pallet is full, the operator can take the complete pallet out and drive it up to the next finishing machine. Again without stopping the printer, so we’re not stopping the printer running. This is a very efficient and productive ways of working, and also very recognizable for many of the customers coming from the offset arena, because this is very similar to what today they’re doing with their offset printers.
Another really new technology is our soft touch gripper technology, which is now implemented in the s25 stacker. Previously all the stackers were using a lot of different belts, basically the belts touching the paper and moving the paper forward into the stacker. What we have done now in the new stacker s25, is get rid of all the belts and basically using small grippers that we wrap the ends, really the edge of the paper very gently and pull it forward until the stopper blade in the stacker and the release it again. Basically we’re not touching the paper anymore. More important, we’re not touching the prints. So this is very;, very crucial for those customers or those applications that require a very, very high ink coverage. A very sensitive high quality prints and high quality or very sensitive papers, like the … Really machine called it media that is more popular now, so and ink head printers. So really revolutionary technology.
Most of our feed is also allow for a by pass, meaning you can either choose to go into the stacker or you can choose to go through the stacker and go in some sort of online finishing, which can be a machine from Tecnau. It can also be a partnering machine, like and Ibu’s or a Horizon, or and NB Folder, or any other machine that you want to connect after the cut. I mentioned earlier a little bit the photo or the photo book area. We have a couple of solutions, one is the page ready, which basically takes a B3 sheet and cuts it down into smaller sheets. This is very popular solution in the photo book arena, where within one stack you have a lot of different sizes of books and basically be reading a barcode, automatically changes the sizes on the fly without any operator intervention.
Very similar solution is the cut ready, or the photo ready. In this case not starting from a sheet, but starting from a roll, so web fat solution. Again, on the fly, changes the different sizes. For instance, in the photo print arena, it allows you to print customer, by customer, by customer. So, 3, 4, 5, different sizes ordered by one customer. You can print in one run and it comes out immediately in the same run. No collection needed anymore.
I skipped two or three slides. No problem. One of the biggest segments today for us, and we are quite successful also in that area, is digital book printing. Digital book printing can be done in many, many different ways. There’s many ways to really produce a book, and every customer we have basically does it slightly different. And every customer we have tells us that he is doing it in the best way. We believe them and we support a lot of different ways. What is really unique in the book printing area is that customers now a days still are batching a lot. So imagine you order four books on Amazon, four different sizes, four different thicknesses. All those thousands of orders are entering at Amazon and then are being batched based on pretty much size. After they have reprinted the different jobs, they need to be collected so your four by four books come from four different sides and need to be collected and then shipped out. What our solutions nowadays offer is the ability to produce order, by order, or publisher, by publisher, or address by address, or length …
We don’t care in what sequence you print because we can handle all different sizes on the fly. So the Libra One book block maker, supports different book sizes, different book thicknesses, two Op and three Op in positioning on the web and on top of that, no white sheets at the back end of your book, by having a variable amount of pages per signature. Really, truly unique. The output of this line is in the end, an unfinished pre glued, book block as you can see in the picture on the right. So that book block still would have to go into a binder and cover needs to be added. We can take it one step further. Then we come to our Libra 800 and that is a worldwide unique, fully integrated book line. Basically starting from a roll, and the end precut is a finished soft cover glued book.
Every single book can be different in size, in cover, in thickness, in number of pages. We don’t care. The machine doesn’t slow down if you have different sizes. 800 books per hour. It just runs through. All based on dot matrix or bar code reading, fully integrated. There is different ways to configure the machine as you can see of those pictures. We have most of the lines running form roll, but also we have one solution now starting from actually B to input sheets with two different input channels and two different cover channels. Again, you can print in any order, in any size, in any thickness and out comes a variable, fully finished book.
Last, but certainly not least, before I let you go and walk around in this wonderful exhibition, some new solutions that we are recently launching for the cut sheet arena. Specifically as you can see on this picture, we have now a whole line of finishing. Dynamic perforating, dynamic punching, dynamic cutting and stacking all in line with, for instance as you can see here, the Canfon I300 cut sheet ink head device. A new line of products. We take the technology that we already have and that we have a lot of experience with, like dynamic perforating, but we’ve now taken it to the cut sheet arena. So it supports a very wide range of different applications as you can see here. The dynamic punching can be done by different cartridges. You can have a two hole or a four hole punch, but you can also use it for, for instance calendars or Y roll finished work. You can actually, as an operator, change those cartridges yourself. So one in the same machine can do different punching applications.
It’s very modular, meaning you don’t need to have all machines in one row. You can have only the cover and the stacker or only the dynamic perforator, or only the prefer, or make different combinations of them. Very soon we will also come out with the same solution but in an offline situation. So starting from a sheet feeder. Not directly connected to any printing device. This allows you as a customer basically to take output from different printers combine it and run it through one finishing line at a slightly higher speed than if you would run online. That finalizes my presentation.
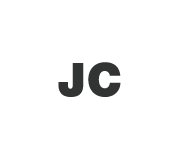

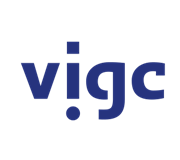

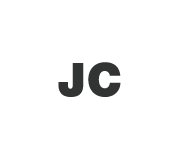

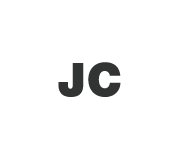

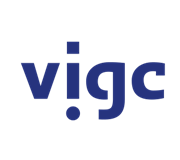

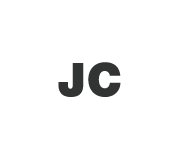

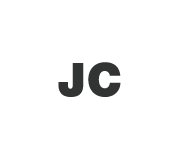

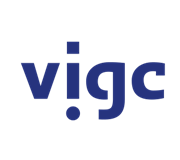

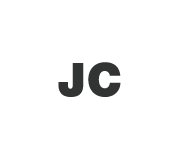
