INKISH.TV proudly presents: Robots in the printing industry
Robots and the history of industrial revolutions plus interview with Henrik Chistiansen from Cool Graphics who deliver robots to the printing industry.
This is a new thing in the robot industry to have co-working robots, with people and robots together. We have that and that will probably be the future.
The productivity will surely increase, because the robot never takes lunch and never goes to restroom.
I am here because the printing industry is looking for the robotic solutions. We are showing some robotic solutions here, and I have other robotic solutions I can discuss with the people here in the show. The robots are mainly needed in the finishing part of the printing industry, because in the finishing department you are having the heavy lifts. So, in the finishing department you’ll receive a lot of pallets full of paper, sheets of paper, which you put into a machine and take out of the machine again after it’s processed. We can robotize all these heavy lifts in and out of the machines. I am focused on the printing industry, because I have experience in the printing industry from press sales, and therefore I know the customers.
The challenge is that the printing industry wants finished products, like when you are buying a car. No printers want to go into developing projects saying this and that, but they want to say: “The product that suits my purpose is here”, and that means we have to develop the product to a real, finished product, like when you buy a car.
If I say, a real long range, I don’t think there will be any place you cannot robotize, but today this is also a question of money – what is more economic, labor or robots? You can also say that in the car industry now, some specific areas are going back to manual work together with robots, because for specific jobs, manual working person is more economic than the robot. But here in the industrial part of the world, labor is much more expensive than robots, for a specific job.
We are now at the company called Stibo Graphic, which is Scandinavia’s biggest commercial printer with web and sheet-fed printing. We are now in the division for sheet cutting after sheet-fed printing. What you see here are some pallets with printed sheets, which we are now going to take to the sheet cutter line. The pallets here are coming out of the offset press for (? 00:05:18) and we take it to the sheet cutter line here, where we would put up the pallet. We have a conveyer system here, where we have to centralize the pallet, and then the pallet is running into the robot, and the robot will perform that. The operator will normally do the airing and separating the sheets.
Yaskawa is a Japanese company mainly producing industrial robots and servo motors. We are a general robot producer. Yaskawa is one of the biggest in the world for that and the volumes, you can say, they are going to the automotive industry mainly. We have worked with automotive for so many years and now we are seeing the opportunity to get into other fields, and therefore the printing industry seems to be very interesting and hopefully important for us in the future.
What is special just now is that we are feeding the vibration table, from its back side. We do that for two reasons – first of all, we have the robot away from the operator area, so it’s a kind of safety, the robot is hidden behind the vibration table; secondly, we turn these sheets in this process and this is because most of the sheets coming out of presses with coding, the coding side is upwards and it has to be downwards in the saddle-stitcher. So, instead of using a pile-turner before the sheet cutting, we have integrated the pile-turning as a rim turning in the process.
The productivity will surely increase, because the robot never takes lunch and never goes to restroom. Now, we have installed this first system with a double-arm robot, here at the Stibo Graphic, and this is the first double-arm robot for the printing industry worldwide, but it doesn’t have special equipment. The equipment around the robot is special thing like the grippers and so on.
Now we are on the other side of the sheet cutter line and the feeder part of it, and behind the feeder is the robot running and what it is doing is separating and airing the sheets, just like the operator does it manually.
What we did with the first one, and what we are doing further on is we establish the test side next to the print shop and let the printer help us, so he can supply pallets to us with printed examples and so on, but we are of course not in the real printing environment. And there is a big difference between testing and being in the real environment, but this is a classic discussion in robot developments. The customers want us to develop the robot to a finish point and we cannot develop the robot to the finish point, without having access to the real environment.
The main body of the robot is to say, for a car industry or a printing industry, but we design the grippers specially for each application and each customer. For example, here at the Stibo Graphic we are trying to design the gripper, so we should be able to handle the paper sheets as the human beings are doing, so it’s very tailor-made.
We have spent more than 3 years for the first one we are having here, but that also depends on the application. This year it was a very difficult application – moving sheets from a pallet to a vibration table, at a sheet cutter line, so it’s big sheets. For the smaller jobs, it could take 6-12 months.
We have partly developed a software in Sweden. We are producing all control cabinets for whole Europe, at our Swedish plant.
This is one of the first co-worker robot-cells in the world. This is where operators and robots work together. To control the robotic process in a sheet cutter line, there are so many various jobs coming through the system that we need a manual input from the operator to evaluate what are we handling just now. This is done by the touch screen here – you can see the cell is here and then we can go into various menus here – we have the robot speed, we have the paper thickness, we can go here, this is about the pile, we can go here, this is about the gripper setting and how we twist the grippers and so on.
I think that in a decent future you will still see a lot of manual labor in the printing industry, next to the robots. And I will add that our robots do not run without skilled graphic operators, because we need to carefully evaluate every job before we start to run it. You have different kinds of papers, printing images and so on, and that has the impact on the temperature of the pile, relative humidity and other things, so we need to have a skilled operator’s input about the job. This is a new thing in the robot industry to have co-working robots with people and robots together. We have that and that will probably be the future.
We require to work with operators who know their trade, so we want to operate with skilled operators from the printing industry. We can educate everybody to operate these robots, but it requires a certain level of motivation from the employee. This has nothing to do with age – there is a lot of middle-aged, mature employees in the printing industry and not so many younger ones, and we can say we can easily educate the mature ones also, subject to they are open to new things. The key is that everything related to robotics will require changes and you must be opened for changes to succeed.
Our aim is to gain more orders for the printing industry and maybe not only for this application with the double-arm robot, there is lots of other places in the printing industry where we can use robots very effectively.
The future for printing industry is fantastic. Everybody says printing is declining, but that’s only if you look at specific sectors like some kind of magazine, especially newspapers, and some kind of brochure. But if you look at specific magazines, special kind of brochures, packaging, flexible packaging and industrial printing – the future is bright.
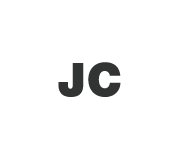

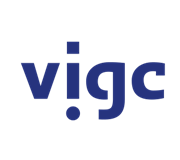

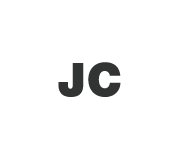

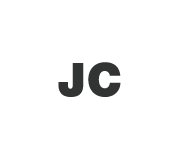

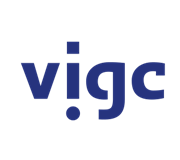

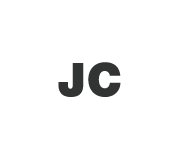

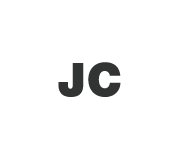

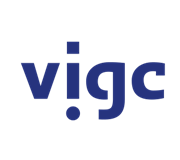

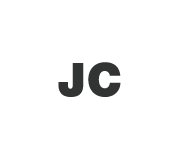
