Product Manager Max Scholz · Ultimate Technographics · Workflow Summit · Stockholm, Sweden
Thank you very much for the introduction. Hello, everybody. Thank you for joining me here today. So far we’ve heard a lot about workflow automation. You’ve heard about the different stages from color pre-press all the way to print. One aspect that we haven’t covered that much is finishing. So what about finishing? That’s what we’re going to do here right.
First of all about myself. I’m Max Scholz. Actually, I’m from Germany but I live in Canada now and I work for Ultimate Technographics which is a Canadian software company based out of Montreal. We were actually one of the first, or actually the first digital and position solution, which is called Impostrips, some of you might have used it or might know it. I don’t know, has anyone in the room used Impostrip before? One. Well, somebody. Two, there we go. So, it’s a company with quite a long history and yeah, lets jump right into it.
So, the market in general is transforming. I think everybody knows it. We’ve heard it a couple of times. Runs are getting shorter, everybody is feeling the pressure. It’s very competitive, the market situation. Where to print is emerging and it’s a really competitive situation and everybody is thinking how can we handle it? What can we do about it? We feel the pressure and on top of that, customers want new types of products. They want high quality products, very short turn around times and they want them customized in the highest quality.
So, first of all, how do you do this? As you might think, the energy is automation here and to automate this, let me show you some data about what is happening in the market right here, what’s the situation when we look at automation.
So, this chart here shows it’s from 2015 comparing it to 2017. So, the numbers are fairly recent and it shows the number of printers that are actually producing their jobs automated. So, the percentage here represents the percentage of jobs they produce in a fully automated manner meaning they don’t touch them at all. They come in for a web to print system and then they ship them fully automated without ever touching these jobs.
So, one thing you’ll notice here in 2015, 61% of the printers were not able to produce the jobs in a fully automated manner. There was not much happening there. They were just not able to produce jobs in that way, but now in 2017, we see a clear trend. So, people are picking up, people are starting to be able to produce a major percentage of their work in a completely automated manner, but another thing you notice here, we still have 32% of the printers that are falling behind, they are not able to produce any of their jobs without touching them.
So, these people, I don’t know if anybody here feels it or he belongs to this group, have the chance or actually the risk of falling behind the other people. So, there is a motivation to look at why is that happening? So, why do people have the problem of automating it? What are the main reasons for them not being able to produce their jobs in a fully automated manner?
So, we also have some data for that. It was a premier study and it’s data from the U.S., but we see a very similar picture in Europe and we have the standard issues that you always see.
First of all, we have job estimation. It’s very hard to do that in a completely automated manner, then right up second is finishing a bindery, which is what we’re going to cover today. We’re going to look at how do we remove this roadblock? How do we overcome the challenge of automating finishing a bindery and then we have a few other things like proofing and approval, billing.
So, there are a couple of roadblocks in the way that are keeping people from automating their workflow completely, but we are seeing progress as seen before.
So, now lets talk a little bit about why would you automate? So, what is there to gain through doing this? I’m going to do this using a use case and the company’s called Cober. It’s one of the most successful Canadian printing companies. They’re actually one of the biggest printers in Canada. They have a very wide range of products. They do essentially everything from flats. They have hybrid production. That means they have digital presses, they also have offset presses. So, they really do everything, but they also provide a wide range of products and services.
So, they’re somewhat an all around printer and they’re one of the biggest and most successful ones in Canada. What was their situation? So, they saw a spike in digital jobs. They had lots of short runs, which they were not really able to produce in a fast enough manner and that was actually affecting their customer base, it was affecting their processes and they were really having issues there.
So, they said themselves they needed to find a solution because the situation was not sustainable and it was actually affecting the customer satisfaction and what did they do? Well, they completely automated their workflow, they implemented automated press press, a complete automated workflow and they automated finishing and this, which we are going to look at later, enabled them to actually finish an average of five to 600 jobs per day, which is a crazy amount and yes, short run jobs, but they were able to actually do that on a constant level with stable quality at a consistent pace.
They had special imposition to minimize waste and essentially, they don’t touch the jobs anymore. It’s just they come in through their online ordering system, everything goes completely automated up to the finished product and then they ship it.
So, in conclusion, as you may think, they were very happy about this outcome and it actually allowed them to grow their business and their experience as they said themselves is nothing dispositive. So, they’re a really good reason that show why would you do this?
So, as you see, you can produce more, you finish more, you have more jobs and obviously that’s what automation is all about, at least you think, but there are a few other reasons why you should automate your jobs.
We heard a lot of this before, but I’m just going to quickly run through what are some other reasons. First of all, you have consistent quality. It doesn’t matter who processes the job or who sets up the equipment, you always get the same consistent result all the time, no matter who does it, no matter when you do it, if it’s weekend, if it’s overtime, if the people are tired, you always get the same results and you’re able to prevent errors. So, if it’s completely automated, nobody can punch in wrong numbers and then miscount them. You’d ruin the whole job, which would need you to reprint it. It would reduce waste through automated layouts and generally achieve a very consistent result of all your operations.
So, in addition to that, you are able to collect data. So, we had a few other talks on that, but it’s a huge advantage because your completely automated system will generate data, which you can analyze and you can see where your problems are the bottle necks, what are the issues in what you’re doing and you can also offer new products.
So, for example, book on demand, book of one. That’s a thing most printers wouldn’t touch. You just print one book, it’s completely crazy. You get the job, you have to prepare everything, you need to process it. You just lose money by looking at a job essentially, but if you have a completely automated production, you can do it because nobody ever looks at the job. You might even have automated shipping. So, it just comes in, it’s processed, it’s printed, nobody touches it, it goes out and you might have a small margin on it, but you might be able to make money and increase the throughput of your machines and the efficient effectiveness of your operation.
So, now, some people may think okay, why would I automate finishing? It takes me two minutes to set up the equipment, it’s actually not so hard, it’s very quick, but if you think about it, if the jobs are getting close, shorter and you get more of the jobs this accumulates. So, as one of our customers put it, even if it takes only two minutes to set up the machine, if you’re processing 2000 jobs, that’s a lot of time. That’s 4000 minutes and it’s about 66 hours. So, you can save a lot of time, which you can use for other things. That was actually an in plan production from a large customer from the financial industry.
So, how do we do this? How do we achieve this? The solution we propose or a general workflow is we have two main products at Ultimate and one is called Ultimate Impostrip, which is a pre-press automation solution and the other one is Ultimate Bindery. Well, what happens in general for the workflow is your order comes in for your MIS or to print system, then it’s directly connected to Ultimate Impostrip, which will take care of the position, sends it to Bindery, which will prepare it for finishing and then automatically prints the job and also finishes the job. That’s just a rough overview so you know what we’re going to talk about, but for example, it doesn’t need to be one machine. It could be various machines. It could be books or for example, do a tune up, then print it, then it goes to guillotine for cutting and then to a binder and three knife trimmer. So, you can automate the whole flow through the system.
So, lets take a very brief look because it’s a prerequisite to do the whole thing at automation, pre-press automation. So, you need automated pre-press. You need an imposition solution that is able to handle barcodes, that is able to handle marks and is able to do that in a completely automated manner in order to even get to the finishing automation part.
Now, you might think it has to be automated impostrip, obviously, because that’s what I’m presenting, but it doesn’t. You can essentially take any imposition solution, the one you might have implemented right now, and connect it to Ultimate Bindery. So, it’s an open system as long as the pre-press solution provides the data, you can connect it. So, for example, Kodak PREPS could be connected and a large number of other solutions that you might have is capable of driving that product.
So, I think everybody knows about imposition and automated imposition. I mean, you take care of ganging your jobs, you do the barcodes and essentially the solution does all that automatically.
So, at Ultimate, we’re all about black box hands off automation. So, what the solution does for you is you set up some sort of rule based layout and then you just have the jobs coming. You either drop them in a hot folder, you receive the XML and they go through the solution. Takes care of your cover page, marks, barcodes, everything for you. You don’t touch it.
So, then, now, we get to the interesting part. So, in order to automate your finishing, what you need to do is you need to link your pre-press to your finishing and that is what Ultimate Bindery’s all about.
So, if you think about it, in order to finish your products, you might need to do the measuring again in order to do the cuttings right, but you already have that data. Why not use it again? You have it in your pre-press department, you created the layout, you put all the marks there. So, you did the jobs once, why would you do it again in order to just do the finishing?
So, what a solution does is it expands your pre-press data, it takes your pre-press data and based on that, calculates the settings for your finishing equipment. So, through that, you can do a couple of things. First of all, you can pre-flight your finishing. So, the solution will actually tell you, “You cannot finish this job. Don’t print it. There is an error in your job. The space is too small. You need more margin here. The paper is too big for your machine,” or whatever it might happen, it will tell you before you print. So, you don’t have to have a mis-run, you don’t need to test it, you know it before you print it and it will prevent errors and thereby reduce waste.
Second of all, it reduces make ready. So, how it works is you set up a so called finishing flow, which is the production line you are going to have. So, for example, guillotine, then binder and then a three face trimmer. So, you set up that flow because you want to produce a book and then a software will simulate that.
So, the transformations of the paper and automatically calculate the right settings for each machine. So, you don’t need to do it manually. The software does it for you. There’s no need to do that yourself.
So, that reduces your workload a lot and I said before, you might think it’s a small thing, it only takes a few minutes to do it, but if you do a mistake with a guillotine for example, it’s very example. You can ruin the whole block and you have to reprint it and I think everybody knows that.
So, lets look at what you can do with it. First example would be automated booklet making. So, this enables you to do is you can print variable size in content, you can personalize content. Essentially, you can do a different product of every job you’re on without even needing to do the manual make ready or the manual set up for that. So, you can do much shorter jobs in a completely automated manner without needing to touch it or without getting any issue there.
We have a customer in Australia … IMC who has implemented that. That’s just an example of how that would be set up.
So, another thing that’s supported is automated cutting. So, instead of, as mentioned before, taking all the measurements yourself manually, preparing all the settings, putting everything in, the software will calculate that and prevent you from making very costly mis-cuts, very costly mistakes and having to reprint the whole stack. So, this is another example.
So, what a customer called iTech did, they implemented that and they were actually able to put out 24% more jobs in a shorter time just by automating their finishing department. So, you can see, various customers gaining huge gains just by not needing to do all those steps manually.
The next example is slitter and cutters. So, you can either have that near line or inline, different solutions out there and most of you might know them. I mean, the examples we have here is a [inaudible 00:14:31] or Horizon Smart Slitter or Smart Stacker and this will enable you to either in or [inaudible 00:14:38] line produce a variable size booklet, books, any content you essentially need is supported for near line, is supported for inline and it will allow you to, again, reduce waste and just streamline your operation.
Another example is the so called book of one. So, a nice example of what you can do with that is there is a café around where you go, you go there, you select your drink, you select your coffee, I don’t know, a cappuccino? And I want to read this book and I want it that format with that font and you order it and when they deliver you your coffee, you also get that book, freshly printed in the back. They print your book as you want it within a few minutes in the back of that café without ever touching it. So, you can essentially order a book on demand just one book and they actually make money with that just by the fact they don’t need to touch it. It’s an inline production, nobody ever touches it and it works for them. Obviously the books are very expensive there because it’s a very cool thing and it’s hip, but it’s just an example of what you can do. You can do also more books, different content, personalized books if you want to print the name of every person that the book gets into the book to personalize stories for your kids where you have the name of the kid as a main character, things like that.
So, the things about our solutions is they’re not limited to any partner. So, we cooperate with a very large amount of partners with a long list of supported machines and we do not choose. So, we don’t limit you to one manufacturer. You can connect, if you like one machine from one manufacturer and another machine from another manufacturer, you can connect all of them through the solution. So, instead of limiting yourself to one brand, you’re able to connect everything. Same is for our imposition solution. It’s not limited to just doing HP presses or xerox presses. It drives all presses. It drives digital, it drives offset so you can essentially use one solution for all your equipment without having any money or things to do with it.
So, lets just quickly look at another case. This company is called RPI. They’re one of the biggest photo book manufacturers and they have been around for quite a long time. They do highly personalized photo products. So, they usually do that for bigger companies. So, for example, a company might have an app where you can order a photo book and those are the guys who print it and they faced a very similar situation. So, they were facing a very steep incline in demand. They just couldn’t keep up and they needed to do something in order to be able to fulfill all these jobs and the interesting thing about this case is they actually gave us a number of by how much exactly they could increase their capacity because that’s something we actually have a hard time getting because it’s very hard to say because they by implementing that automated finishing workflow increased their capacity by 25 percent by even using less manual labor in the process.
So, they produce a lot more, but with a lot less manual steps. Yeah.
So, what’s next for us? We are actually at various events all around the world. The next one is in Australia I think and if you like, it would be great if you follow us on Facebook around. If we see you at one of the other events, it will be great and if you have any questions, I was a bit too fast, I’m sorry for that, now would be the time. Oh boy.
So, I know it’s all soon, but it’s good. We got it out of the way. We thought this would be an interesting topic because we all know that the depart of retention part is very often [inaudible 00:18:39] and if you really would like to start a hand off workflow, that is into inspiration, that is easier, right? Like Amazon and [inaudible 00:18:52] in May and as we were doing this, he said okay, [inaudible 00:19:05].
So, he said you should talk to these guys and that’s why Max is there and this is exactly how we would like to do it. When we do this [inaudible 00:19:29] we really like to catch all the angles. If we miss an angle, we won’t do cuts, but this area should be very interesting for all of us because we all know that the product is not ready until it’s finished.
So, are you saying the-
Yes, I’m staying for dinner.
So, you’re staying for dinner, which means if you don’t have a question now, you can always grab Max later. This, I would really encourage you that they have done some very cool [inaudible 00:19:59] with customers and this is [inaudible 00:20:03].
There is a question.
How do you carry the information to the operators because some of these machines doesn’t have an automated interface where you can shoot in-
So, of course-
Sure. The question was how do we carry the information to the different kinds of equipment because not all of them have an automated interface.
So, there are a couple of ways we do it. First of all, of course, there are some requirements for the machine. So, we do not support every possible machine. So, the machine needs to generally be able to handle that kind of workflow. So, how would it would actually work on the job floor is you would print the job if it’s near line and the operator would take the stack, put it into the machine and scan the barcode and according to that barcode, the machine will then setup. So, that’s how it works.
So, you scan the barcode, it fetches all the settings, does make ready and then produces it. So, one very important thing I forgot about telling you is how we do this is we work very closely together with those manufacturers in order to get the drivers right for all of the machines.
So, it’s a long process of testing out everything, getting all the specifications for the drivers right and to make sure that it will actually work and take the ease of implementation off on your sign because you might think it’s very hard to connect the machines to those things, but we actually take care of that before we do produce the driver specifically for each machine and then it’s just a matter of putting the address of the machine there and checking a few boxes in order to run the machine in an automated manner.
I will maybe rephrase the question or maybe to add-
Sure.
What to do with a machine that’s lets say a semi-automatic or lets say that half of the machine should be manually set up. So, how then what is your solution to provide the information for the actual operator that needs to actually do some manual work? Because the machine is not setting up automatically.
So, as I said, there are some requirements to run the machine through the system. We do support so called generic machines. So, if you have one machine in your workflow that you cannot integrate, you can simulate that machine on that generic driver. So, it will do the calculations and simulate the paper transformation for you, but obviously if the machine cannot be connected and is not able to read any data, we cannot connect it to the workflow.
So, you will in that case need a machine that is able to actually communicate or at least take the barcode for that workflow. Okay?
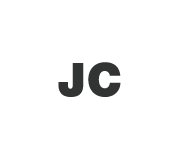

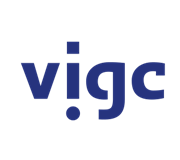

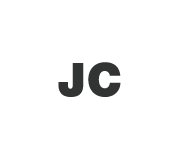

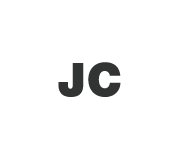

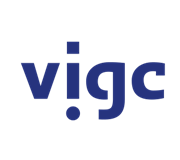

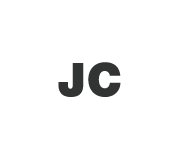

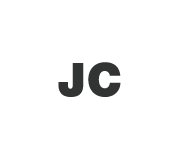

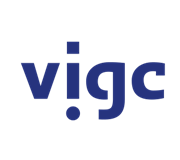

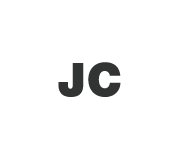
