Moving LED-UV to the next level · Steve Metcalf · AMS Spectral UV
The impact LED-UV has had on the printing industry the last years is simply amazing. AMS – now AMS Spectral UV – was one of the early adopters in this technology and not only have the technology developed rapidly when it comes to quality, pricing, and even the spectra where the UV-light operates, but the applications and equipment using UV has increased a lot. Having broader frequencies makes it possible to have fewer photo-initiators in the ink making it both cheaper to buy, but also better for the environment. UV has so many advantages, and though the ink is still more expensive, the advantages surpass this.
AMS Spectral UV now takes LED-UV a step further by offering to retrofit LED-UV on web-offset presses. Exchanging the gas heater with LED-UV saves gas, electricity, but even increase the quality of the print beyond what’s possible with the gas-dryer.
In this film, President Steve Metcalf explains the opportunities!
So in the position we’re in and we’ve had a fantastic amount of success getting the LED revolution from sorta its infancy early on to a point now where it’s relevant technology on any machine, the fastest machines in the world now. So our focus is now looking into what’s next, okay. What’s next in terms of the speeds we can achieve on presses that are not just the fastest sheetfed perfector presses in the world or the straight presses, but the next level which are web offset machines that can run at double the speed of the fastest sheetfed perfector. So it’s the powered levels, the LED efficiency that’s needed, and the technology to support that process. It’s a big theme for us this year.
Another thing we’re doing is, it’s very exciting, is adding more intelligence to the process. A lot of our customers are coming now with such a revolutionary process with LED curing, the kinds of intelligence they can get for quality assurance, quality control to provide that assurance for their own downstream customers. As we get more into the packaging industry we’re seeing quite a lot of this or very sort of highly efficient, highly optimized commercial printing environments. So we’re bringing new intelligence features into the systems that we’ll be talking more about as we roll into next year.
Well it’s a combination of several things that we’ve done. One is is we’ve got a patented technology to provide the most amount of intensity anywhere to the sheet or the web. So we’re bringing a lot of LED light intensity very quickly on to the materials. And as the speeds of the machines have grown so too has the power that’s available for the process. And we’ve put a lot of energy into developing that into very compact footprint at very reliably so that you can really run with a single LED unit for most of the presses is all you need to get this process started.
We also pay a lot of attention to the ease of retrofitting this into the existing machines. So it’s a much simpler way to go when you think about the UV or the LED process compared to traditionally what we had to deal with. So customers now can switch to an LED system on a conventional press, an offset litho press, sheetfed perfector, web offset LED of any type. And the installation is made very quickly because of how easy it is to bring this technology to bear.
So retrofitting, you can think of it in sort of two parts. One is the electrical mechanical idea of retrofitting a machine and we have a tremendous amount of experience. Our company specializes that. We lead that activity in the world. But the other part of it is the process. It’s converting the process over. One of the things that we do is we offer a secure cure guarantee that anything we show somebody in our LED look book, if you have the right ingredients for the process and if you set it up properly you can achieve that. You can achieve the densities that are in that book. You can achieve printing on those substrates and materials that are incredible value. You can achieve the coating effects that are available now for these machines. So we offer this beyond just the retrofitting of a piece of equipment, but all the way through the process. And we consult with customers while they bring it into production.
We’ve seen every type of machine. We’ve seen every type of printing application that can be done. We’ve seen all the materials. We know all the inks available on the market. The coatings that have become available for the process. And we really know how it all fits together. And that’s one thing that we do that sort of separates us from a lot of the things that are starting to happen in the market. You hear about LED all the time now and there’s a lot of people that are joining the party. But we really enjoy that advantage because we’ve understood the process from the beginning, we’ve worked with all the major suppliers of all the ingredients for the process, we’ve seen it on every machine. And so that … We wanna continue that as we go. But there’s a lot of exciting things that are happening. And as we start moving to the Drupa in not even two years, there’ll be even more announcements of advancements that will continue this revolution of technology.
It’s incredible. We’ve already done quite a few of these installations. Started in Asia, in Japan. We’ve done them in Europe. And now we’re talking to plenty of printers here in the United States. The ROI, the return on investment, for a web offset, especially a heat setup for commercial printing, to move it into LED and eliminate the heat set dryer and eliminate the gas to zero, eliminated the electrical consumption by at least 50% and get rid of all the quality problems that had ever existed on a high speed commercial web, it’s astounding. That you could do it in a space about this wide. A lot of our customers are reclaiming that dryer space and the chill down space. And they’re going instead with new finishing equipment at the same time. So they’re adding more value to the process, but they’re getting the output that looks as good as the highest end commercial printing you could ever find on [inaudible 00:05:19]. You can’t tell the difference between the sheetfed process and the web process anymore.
Your web offset machines it’s been an incredible capital investment just to get them where they are. And to be able to bring technology, new technology that can transform them to match the requirements of today’s production, a shorter run lengths, higher quality, multiple material types, all these things. It’s a lot of fun because these machines will say in the industry for many years. And if we can bring additional things to enhance them it’s a great opportunity for us and it’s real. We’ve got fantastic samples that we show people that really bring it to life. The types of paper, the types of ink densities, the quality level that’s there, it’s really fantastic.
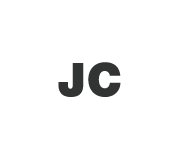

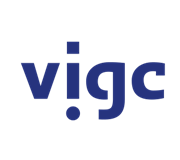

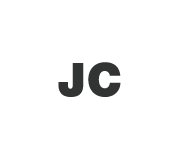

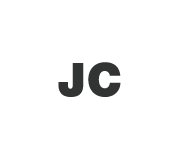

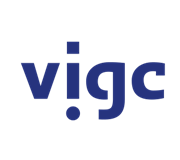

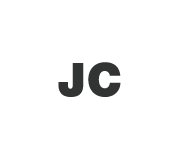

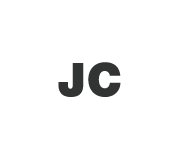

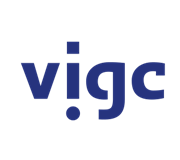

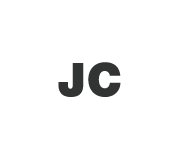
