Textile Print in the Center of the Mega-Cities · Danny Gazit · VP & GM, Direct to Fabric · Kornit
Kornit is one of the leading suppliers of DTF and DTG. In this film, which we did in Israel (as you can see from the drone shots in the beginning), we talked to VP & General Manager, Direct to Fabric, Danny Gazit, about how this at all is possible. But see and listen for yourself. Great insights!
Kornit deals with digital printing. An innovative company that is dealing both with the DTG, direct-to-garment world, and the DTF, direct-to-fabric world. We’ve been in business for the last 20 years, direct-to-garment. We’re one of the biggest players in the market today, with customers all over the world and offices all over the world.
Around five years ago, we’ve gone into the direct-to-fabric market with our Allegro machine, which has acquired quite an intensive install base since then. And then last year, at ITMA, we have announced the Presto. Presto is the new generation of the direct-to-fabric machine. It’s being used in quite a few places, has a very good market traction, and is being used in extensive markets around the world already. We’re quite excited to see how it’s developing and how it’s moving along.
Let’s look at the subsegment that we’re speaking about, which is digital printing. Kornit supplies an end-to-end solution. We can integrate with different types of free software, different types of cutting machines, sewing machines, et cetera. And in terms of the solution that we provide, we provide our own ink. We provide the technology behind it, and there’s tons of engineering and technology all the way from how we handle media and types of media that we can handle through the chemistry and what type of substrates we can print on, all the way to the curing and how it goes out of the system.
And we position ourselves both as a close solution provider [inaudible 00:02:07] brings to the table unprecedented inks that are not found anywhere else in the market, a technology that is extremely user-friendly and can be operated by a single operator, and qualities of prints and resolutions, ability to recreate digital files, and also recreate different types of designs that you have done before, which is unprecedented.
When you look at the analog and the classical production methodologies, you see that there’s a different way to apply ink or dye to different type of fabric. Roughly speaking, we’d separate the world into natural and synthetics, where synthetics are classical sublimation, mostly by heat transfer, meaning we print on paper and we [collander 00:03:02] it onto a fabric, and on the natural side, you’d find reactive inks, which require quite a heavy process of pre-treating the fabrics before, and then steaming the fabrics afterwards and washing it. It’s both chemically extensive, water extensive, and most of all, energy extensive. And it also find the process which is called acid, which is used on protein-based fibers, such as wool or such as silk, which is similar to reactive, but a different type of ink.
The classical implementation is the pigment implementation of taking solids, pigments that are in a dispersion, and applying them to the fabric. That had been done in the analog world, and today, in the digital world, it’s quite complex to do that because of passing a solid within an inkjet. That’s not something that is trivial to do, but we have, at Kornit, mastered this type of printing technology, and furthermore, when you look at how pigment is applied, usually it needs to be applied to a fabric which is pretreated, or else the ink will disperse into the fabric and we lose resolution and printing quality.
We have managed to find a different solution where we actually fix it, the ink, before it hits the fabric, meaning that it will not dissolve inside the fabric, but will be applied on top of it. And we’re able to do that with a wash and rub fastness or durability which is not found in the market anywhere else.
Let’s talk about the cycle of transportation, for a second, that goes into the textile industry. This is just to give you a taste. You create screens somewhere in the East. You bring them back after you created the design. You do a sample. The sample is good. You go back to the factories that are somewhere far away, you create 10,000 meters, 20,000 meters, whatever you want. You ship them back through. Just the amount of shipments that I passed on, back and forth, on this time is time-consuming and also has a large impact on the environment.
Now, what if I can print in the middle of New York or in the middle of Los Angeles in a very clean environment, within a very small footprint, with one operator behind it, and can get out the prints? All I need is blank fabrics. Those are the only things that I need to bring over.
Suddenly, there’s no screens, there’s no back and forth, time run are being cut very short, and the impact of moving, and you know that air transportation today is probably the highest impact, and sea transportation is probably the highest impact on the environment that we have today. Suddenly time and the impact on the environment is saved. So, we see a trend of moving to nearshoring.
A few of the systems that we’ve sold in the last period of time… I’m talking months… have been sold to places which are printing center of megacities, not even villages and so on. And I think this will become a very strong trend, this time, we pass on, because it makes a lot of sense.
Yeah, I think so, also, and I’m very excited to see what is coming up. I don’t think that there’s any value proposition out there in the market which is able to print on all substrates, which is able to print with inks which have such a wide color gamut, as you see around here, and durability for both wash and rub which is unprecedented in the market today. And for me, that makes a lot of sense in where we want to go today, and the markets that we want to go today, with our digital printing.
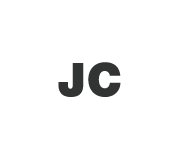

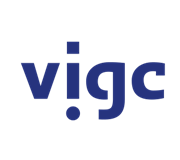

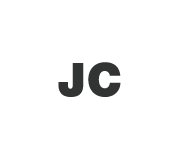

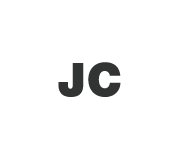

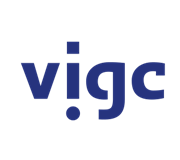

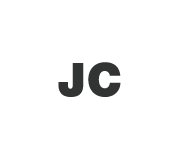

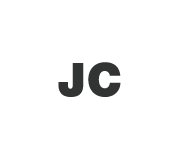

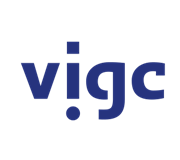

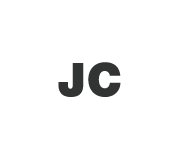
