Industrial Scale Digital Print Enhancement · Jürgen Stocker · Head of Sales & Product Management
Made in Switzerland is highly relevant for the international print industry. With precision, passion, reliability, efficiency and a wealth of experience, not only very good print productions arise, but also innovative technologies.
Jürgen Stocker, Head of Sales and Product Management at Steinemann DPE AG in the canton of St. Gallen, answered questions from Andreas Weber, CEO INKISH D-A-CH. It was about so-called “Enhanced Digital Print Solutions”. This refers to possible innovative refinements for sheet-fed and reel-to-reel productions based on inkjet technologies. It is exciting to see what has happened here and where we are headed.
By the way: Steinmann DPE AG has been part of the successful international enhancement specialist Leonhard Kurz Stiftung, based in Fürth, Germany, since 2019.
—
Made in Switzerland ist für die internationale Printbranche eine gesetzte Größe. Mit Präzision, Leidenschaft, Zuverlässigkeit, Effizienz und reicher Erfahrung entstehen nicht nur sehr gute Print-Produktionen, sondern auch innovative Technologien.
Jürgen Stocker, Head of Sales and Produkt Management bei Steinemann DPE AG im Kanton St. Gallen, stand Andreas Weber, CEO INKISH D-A-CH Rede und Antwort. Es ging um sogenannte „Enhanced Digital Print Solutions“. Gemeint sind damit auf Basis von Inkjet-Technologien mögliche innovative Veredelungen für Sheet-Fed- und Reel-to-Reel-Produktionen. Spannend, was sich hier getan hat und wohin der Weg geht.
Übrigens: Steinmann DPE AG gehört seit 2019 zum internationalen erfolgreichen Veredelungsspezialisten Leonhard Kurz Stiftung mit Sitz in Fürth, Deutschland.
LinkedIn Profile: https://www.linkedin.com/in/juergen-stocker-a4706186/
Now we have offline in the industry – offline solutions. But an integrated in-line solution, like an integrated varnishing unit – inkjet varnishing unit – nobody currently offers in the market. I think this is the next big thing.
What is Steinemann DPE?
Steinemann DPE is producing machines. Machines for print enhancement and nowadays for digital print enhancement. So we have built and sold over 900 machines for analog print enhancement and now we do it for digital print enhancement. For sheet-fed printing machines and reel-to-reel printing machines. And this is here now in St. Gallen. This is the technology center where we develop and build these kind of machines. Digital print enhancement means we have digital varnishing and digital metallization technology.
We use inkjet technology for our machines. What is special at Steinemann DPE. DPE stands for digital print enhancement. So we are 100 percent daughter of Leonhard Kurz Prägefolien. And this is special because with that we are a full-system-solution-provider for our customers. This means we have machine, service and all consumables coming from one hand – from Leonhard Kurz. And Leonhard Kurz takes care of everything.
And how long is the relationship with Kurz?
So the acquisition of Steinemann DPE was on first of June 2019. And before Steinemann was part of the Steinemann Technology. And now Steinemann DPE is part of Leonhard Kurz.
Are you still partnering with Steinemann?
We are still partnering. This is correct. We have a very good relationship. So we use the infrastructure of Steinemann Technology. This means if we need people who assemble the machine, if we need people for manufacturing our machines. They do it for us. So we can take it, if we need it. And if we don’t need it, we don’t have to use it.
Are you also partnering with other industry suppliers?
This is an open partnership, as you see it also on the website. We have the Ricoh printheads which we use in our machines. And the partnership with Gallus is following: we are OEM supplier for Gallus with our technologies. So we have a digital embellishment unit, which Gallus is using on the Labelfire machine. But we are also an OEM supplier, with the Printbar White, which Gallus is using on the Labelmaster machine. So it’s not only varnishing. It’s also white as an embellishment possibility.
What kind of people work here and what is their expertise?
So we have mainly inkjet specialists here who know how to to handle all these inkjet topics. And of course, we have also people here in our company who know solid Swiss made machine building. As you can see here, there is a machine here beside me or on the other side, it is the original machines like that. They are 30 years in the market and still running in the market. So these are really solid Swiss engineered and built machines. So we have technical experts on a very high level here who are working on the details. And now it comes as we are part of this Kurz Group. We get also resources from Kurz. So if we have some specific needs and some topics, we can get these resources and experts also from the Kurz headquarter. And especially with the foils obviously metallization, everything is really adjusted to each other. Everything is made perfect for each other. And this is only possible in a – OK, we have the experts here – but we are part of a bigger company as we are in the service area. This is only possible to be one part of a big and good working company.
What can we see in your customer experience center?
We have currently here in our demo center, we have two machines. So we have a machine here on the right. It’s a 76 machine with a B2 format size. And here the 106 machine in the B1 format size. This is also the machine, which shall be our DRUPA machine. And we make customer demonstrations here. We make customer shows here. We make samples here. We make R&D work here on our machine for continuous improvement.
What are the main benefits if a customer chooses Steinemann DPE?
As I would say, the customers for our machines they like very much the industrial approach of our machines. As we have machines which are really for industrial printing. So we have some machines in the market where you can do a single pass application. Means varnishing and metallization in one run on the machine. We have some machines which have the highest speed. You can run in perfect condition, up to 7000 – 7000 sheets per hour. And you can do nice applications with a possibility of gray scalation. That means you make high-ink laydowns, low- ink laydowns in one run in the machine, which is very useful for the customer. And last but not least, we are the one in the markets where you can have a low grammage application . Means we start from 4 micron up to 100 micron ink laydown which is very important for customers because low-ink laydown is very important if you want to do further converting on cardboard, for example.
Who are your customers?
We have customers in web-to-print. We have customers in packaging, in cardboard packaging. And we have also customers, as I mentioned, in reel-to-reel. So we have installations all over the world. We have installations in Asia. We have installations in Europe and in the U.S.A. So we have a global footprint and especially as part of the Leonhard Kurz, we can ensure the customer now that he gets in his country the perfect service and support, application support, what he needs to run our systems.
How do you go about from development to a finished machine?
It’s like on other machines. We have different components which we bring together and we make it work together. So we have the varnish, we have mechanical components, we have electronic components, we have softwares which we bring together on the machine. Which we can realize together with our partners, that they’re working robust and working stable also for industrial printing. So our reference customer in Germany is, for example, Flyeralarm. So they are working on the high seasons for shifts per day on both machines. They have two 106 -machines. And on the high seasons they are really running the machines and get in their files in, in the evening. PDFs as you mentioned it. They print it and in the next day they deliver it to their locations. Where you can pick up your business cards, for example. And I think this is important that you as a machine supplier, a full-system-solution-supplier realize, together with all your partners, a solid and working machine base which ensures you that you can fulfill the promises which you make as a printer. Order today, you get it the next day. This is the important thing from our point of view.
Who was inspiring who in your relationship with Flyeralarm?
It was really a little bit like that – that they approached us and asked us if if we could imagine to build such a kind of machine because they knew our analog machine systems, which they had also in their production. We thought about if it would be possible to integrate the new technologies, the inkjet technology in the analog machine systems. And this was at that time our task. Which we successfully fulfilled.
No risk, no fun?
Yes, I would say so. Because after 2008, Steinemann Technology as a former company which owned Steinemann DPE. So it totally stopped with building analog print enhancement machines because their market totally collapsed. There was strong competition from Asia. There was strong competition from Europe. But with the new inkjet technology and with the specific knowhow which you need in this kind of complex technology, it makes sense again to build or rebuild or to start a new machine, systems like that, and build it again in Switzerland. Yes.
When did you switch to the inkjet technology?
We installed the first machine in 2014 at Flyeralarm. This was also our first machine which we installed. So they have been our first customer. Therefore, we have a special relationship with them. Because they have been also our reference customer at that time. At that time, we installed only a varnishing machine. And after the DRUPA 2016, we enlarged this varnishing machine with the metallization possibility. And now they have a 106 where they can do the varnishing and metallization. And the second 106. It was installed in summer last year. They have also both possibilities on that machine.
What is the next big thing in digital print enhancement?
I would say the next big thing is maybe an integration of digital embellishment solutions. So let’s let’s separate the industries. Let’s say we are in the sheetfed printing industry and in the narrow web printing industry. And I would say the next big thing in the sheetfed printing industry is an integration of embellishment solutions, in-line integration and digital printing machines. Kba office machines or HP in sheetfed printing machines, integrated solutions with digital embellishment. I think this is the next big thing. Because now we have offline in the industry – offline solutions. But an integrated in-line solution like an integrated varnishing unit – inkjet varnishing unit – nobody currently offers in the market. I think this the next big thing. Or an integrated digital metallization solution, nobody’s offering currently in the market. I think this is the next big thing. And in the narrow web I think, of course, the integration of the embellishment solutions not only on digital printing machines, but also on analog printing machines. So you can use the advantage of digital technology on short runs on your analog printing machine. Because we have in the market still a lot of analog flexo printing machines which run their short runs but the embellishment is very expensive. And then they do it offline in a converting line. So I think this is the next integration. In my point of view.
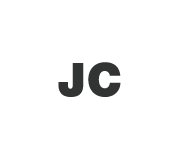

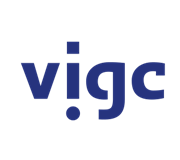

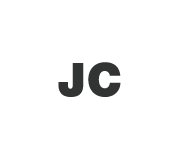

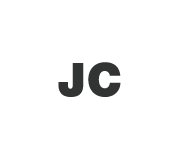

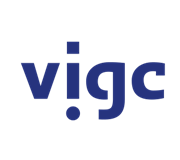

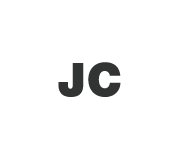

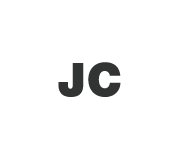

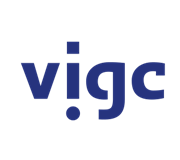

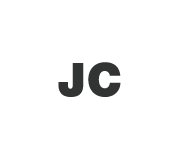
